Haven't submitted your best work from 2015 to the Core77 Design Awards yet? What are you waiting for? You have until March 8th to submit while the regular pricing is still in effect, and the absolute final deadline to enter is April 6th, but we all know how time flies. For a little extra motivation, get to know the folks that will be critiquing your work in the first of our four-part interview series: Meet Your 2016 Core77 Design Awards Jury Captains!
Part one introduces the esteemed captains of the Open Design, Packaging, Furniture & Lighting and Service Design categories and asks them each a few questions about their design practices.
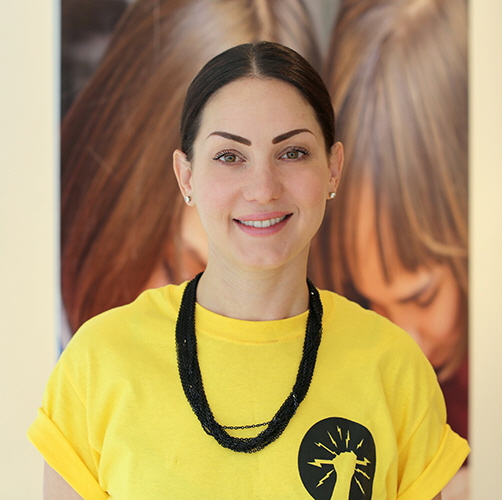
Bethany Koby - 2016 Open Design Jury Captain
CEO & Co-Founder, Technology Will Save Us
Bethany Koby is a mom, designer, educator and the co-founder of Technology Will Save Us. Technology Will Save Us is on a mission to spark the imagination using hands-on technology. Their beautifully designed DIY Gadget Kits and digital resources are the most accessible way to make, play, code and invent with technology.
What do you see as the most significant changes/developments in Open Design/DIY in the past few years?
The maker movement is growing and over the last few years we've seen a lot of maker businesses growing and expanding. Personally, I think it's a need for tangibility, in a world where so much of what we do is on a computer or screen, people are looking for something they can create that they can touch and feel. Digital making is bringing these two things together, the screens that are everywhere around us, the excitement of creating something that you can hold in your hand, and has an impact on the real world.
Cathy Davidson, a scholar of learning technology, concluded that 65% of children entering grade school this year will end up working in careers that haven't even been invented yet. We think kids will invent future jobs based on playing with Minecraft, making thirsty plant detectors in their kitchens and designing their own games controlled by their micro:bits. This is why Tech Will Save Us is focusing on sparking the creative imagination of young people using hands-on technology.
What do you think is the greatest misunderstanding about Open Design and DIY?
We talk a lot about kids and they are at the forefront of everything that we do and create. But really this is for everyone. We want to create a generation of makers, but we also want to influence everyone to pick up something that is broken and learn how to fix it. The impact of having more switched on kids will touch everyone, and will affect our lives in the futures.
We wanted to create a brand that invited people into the world of technology and helped them to feel empowered and confident around what they potentially would be able to make. Realizing that you can create circuits using really simple materials, and then creating really interesting beats and bespoke music using that synthesizer and other things in the house—that could unleash a whole understanding of a hobby or profession. It doesn't matter how old you are, that's a really satisfying experience.
What serves as your greatest source of inspiration these days?
Users inspire the work I do. Young people and the adults that love and support them give me inspiration and insight around new themes, skills and possibilities I could have never have imagined. Our awesome team also inspires my work. We have an incredibly talented, passionate and dynamic group that continually invent and create experiences to delight and surprise me always!
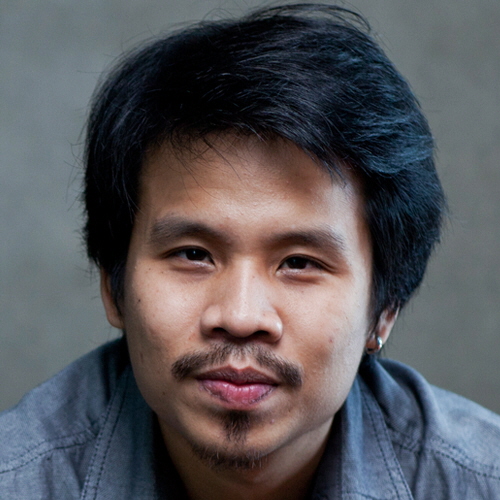
Somchana Kangwarnjit - 2016 Packaging Jury Captain
Founder, Prompt Design
Somchana Kangwarnjit graduated from King Mongkut's Institute of Technology Ladkrabang with a degree in industrial design. In 2009, he founded Prompt Design, helping his clients to build brands and businesses by delivering new experiences in strategies and design executions. Prompt Design's clients include Nestlé, CP, Singha Corp, Pfizer, FrieslandCampina, Diageo Moet Hennessy, BJC, etc. He is regularly invited to be a committee or jury member for design competitions and often serves as a guest columnist and professor for many publishers and top universities.
What do you see as the most significant changes/developments in packaging during the past few years?
The online world has been more and more important style of living in the past half decade. The packaging will not only be a simple package with limited space label and box. More information and tactics like QR code, AR/VR technology are applied to it. New packaging development will be more advance and tends to combine some media onto it to make a viral campaign. Therefore packaging has to be continually evolving both in terms of technology and distribution and certainly taking care of our planet.
What do you think is the greatest misunderstanding about packaging design?
Many people misunderstood that TV advertisement has more influence than packaging presentation. There is a research showing that the buying choice influential for food product is 40% more and also for wine choice is 46% more with packaging. This is a proof that packaging design is very important as well.
What serves as your greatest source of inspiration these days?
Looking back into the history of packaging and advertisement at each period and time may be helpful in forecasting our future trends in packaging and design.
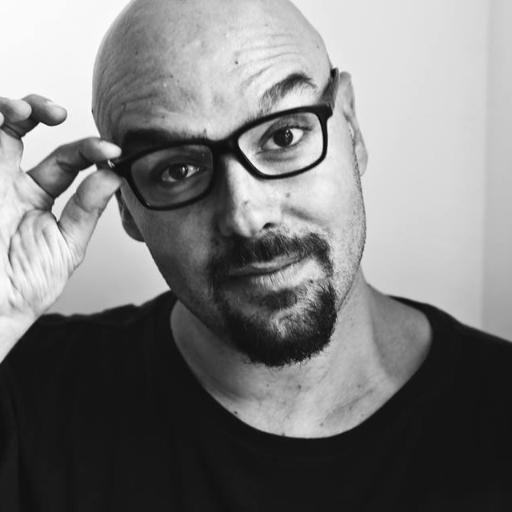
Luca Nichetto - 2016 Furniture & Lighting Jury Captain
Founder, Nichetto Studio
Luca Nichetto was born in 1976 in Venice. He studied at the city's Istituto statale d'arte, before undertaking a degree in industrial design at the Università Iuav di Venezia, from which he graduated in 1998. In 1999, Nichetto began his professional career with Murano-based glass maker Salviati, later becoming a product designer and consultant for lighting company Foscarini. In 2006, he founded his eponymous practice in Venice. In 2011 he moved to Stockholm, Sweden, to open a second studio and he continues to live in and work from this city. Over the course of his career, Nichetto has served as art director for many international design brands and he has developed an in-depth knowledge of the design industry.
What do you see as the most significant changes/developments in your field in the past few years?
There is a big difference between the way various designers in different locations approach the design and manufacturing process. I think Italian design is famous for its connection to the manufacturer, and an approach that all the time pushes for experimentation. It's where I'm from, so it's in my DNA and everything. This industry, in Italy, is not built for mass production, but more medium size, which really help to develop and increase your knowledge doing new products and new projects. In that sense it helps the connection between the designer and entrepreneur. You see more family run companies in Italy, and designers who talk more about projects, follow their gut and instincts, rather than what the market or some marketing guy tells them. This helps challenge things in the industry. There's a totally different approach in Sweden, which I found much more American when I moved there. Rather than just talk to one person about a design, it's a team of people. I'm not saying one approach is better than the other, but experiencing both helped me adjust my point of view so I'm not always pursuing ways to create iconic or emotional pieces.
Discovering the Scandinavian world helped me also to understand and to try to clean a bit my design and to be more focused also on the functionality and the respect for the environment. For example the environment point of view is something that I really started to appreciate much more when I move here. Before it wasn't something that really connected with the Italian design. Not in a bad way, but it was not one of the skills that was required for a design. In Sweden it is much more Scandinavian so you start to look at things differently, which for me, in the beginning, was a big challenge because that means you need to change your approach. Eventually it became like a kind of mindset, so right now, for me, it's kind of easy... it has become part of my way to do design. To be a designer is one of the most beautiful things because you can learn by doing your job. And so it means that you can learn all the time and your design always constantly developing.
What serves as your greatest source of inspiration these days?
Yeah that is the kind of question that is very difficult to give an answer because personally I think inspiration is almost everywhere. You can read a book you can watch a movie you can listen a song. So to be honest I think inspiration is a match for me between what I know, in terms of knowledge, means what is possible to realize. So know the limit of production. And eventually knowing that push that the supplier or the factory to try to improve to try to experiment. And to the other side to be curious. I think the curiosity is the thing that make you inspire for many things. Inspiration could be in a candy or really could be everywhere. There are no one thing that just I can say, "this is absolutely the only that gives me inspiration." Would be sad if it was like that.
What are you most looking forward to seeing in the entries of the Design Awards this year?
I would love to see the knowledge of people if they are able to express in their project what is a good idea. And a good idea for me means that they need to understand if is possible to realize that. I'm not a person that is looking just to if the shapes or is fine is cool or whatever. I want to see if what they are designing is also, they thought that it is possible to be realized. Personally I think design is always connected with industry. Otherwise we would be artists. So if the design need to be connected to the industry to exist, the designer need to know something about industry to exist. If you don't know you are not a good designer and your idea is not good enough. So that would be probably the main things that I will check.
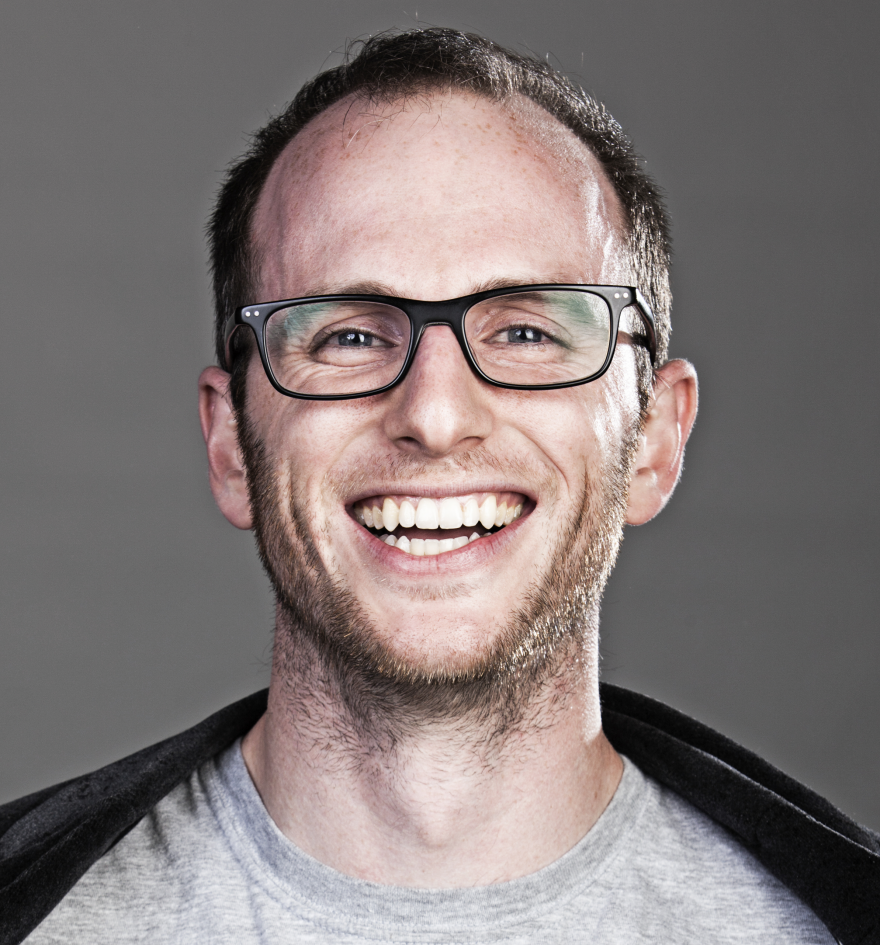
Joe Gebbia - 2016 Service Design Jury Captain
Co-founder, Chief Product Officer of Airbnb
Joe Gebbia is a designer and entrepreneur, and is the co-founder and Chief Product Officer of Airbnb. In 2009, Gebbia was listed in BusinessWeek's Top 20 Best Young Tech Entrepreneurs. In 2010, he was named in Inc. Magazine's Thirty under Thirty, and 2013, he was named in Fortune Magazine's Forty-under-Forty.
What do you see as the most significant changes/developments in service design over the past few years?
Design has the potential to move beyond objects. We're all taught in school that design is more than look and feel, that it's the whole experience. Given that we're always on, connected by a device to the internet, the practice of service design is highly underrated. There are so many touch points into products and service systems that you can't focus on the design of just one moment without considering the entire scope of the experience. In the future, I believe design can serve even higher callings, such as designing more trust into people's lives.
What do you think is the greatest misunderstanding about service design?
People think design is only about style, that it is just an aesthetic afterthought. When done right, design considers everything.
What serves as your greatest source of inspiration these days?
Recently, I visited the Martin Luther King Jr. center in Atlanta. His birthplace home, tomb, church, museum, and neighborhood he grew up in are all located within a two block radius. In learning about his life from beginning to end, I could see someone who beautifully communicated a vision that was much bigger than himself. I would highly recommend checking it out.