Currently Crowdfunding: An Ergonomic Armrest, a New Halfbike, and More
These Tables Look Like Marble, but They're Made from Denim
Plott's Nifty AR-Based Tools Help You Design, Measure and Create with Accuracy
Design Job: A New Career Frontier: Rockstar Games is Seeking a Digital Designer in New York, NY

Rockstar Games is seeking a talented and dedicated Digital Designer to join the Marketing Department at our NoHo, NYC office. The ideal candidate is a multi-disciplinary designer that has very strong design skills and a deep understanding of the advantages and limitations of digital media to create
View the full design job hereDesign Job: The Future Perfect is Seeking a Product Development Coordinator in New York, NY
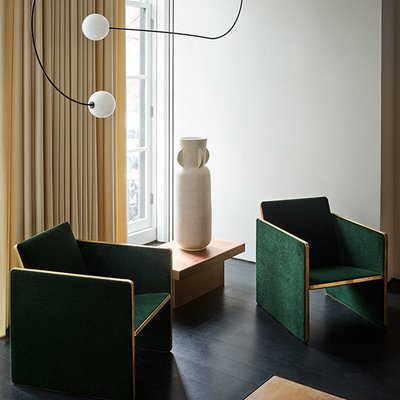
The Future Perfect is seeking a talented creative individual to help guide the success of it’s in-house furniture and decor collection. The position will offer the right candidate to work directly with ownership and current celebrity and up and coming design talent. This exciting position offers travel opportunities, exceptional influence,
View the full design job hereReader Submitted: Already Tired of High Maintenance Shared Electric Scooters? This Autonomous Version Takes Care of Itself so You Don't Have To
Rol is the scooter that comes to you. Equipped with autonomous technology, Rol drives to pick you up. After taking care of you, it takes care of itself. Driving itself to recharge, relocate, or park, Rol is a self-sufficient progression of today's shared electric scooters.
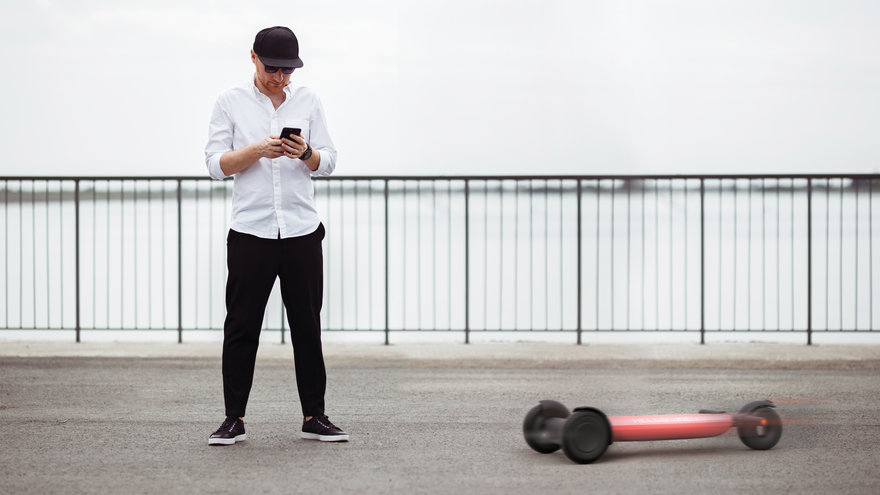
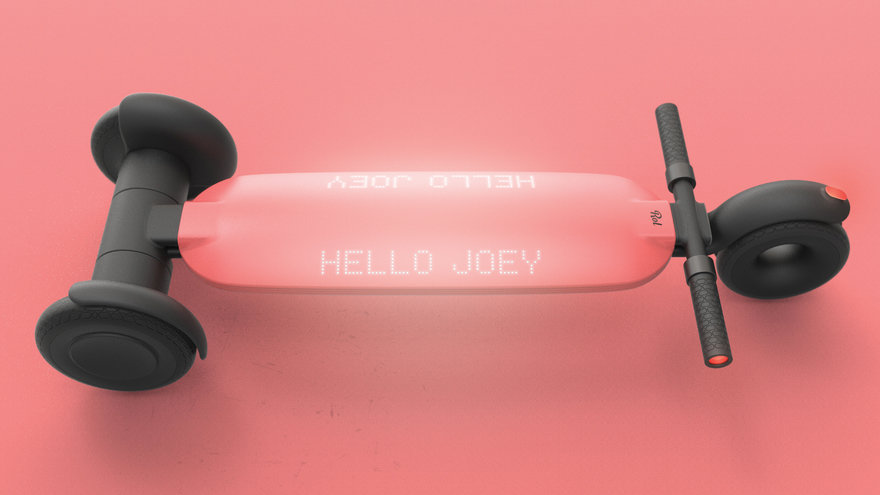
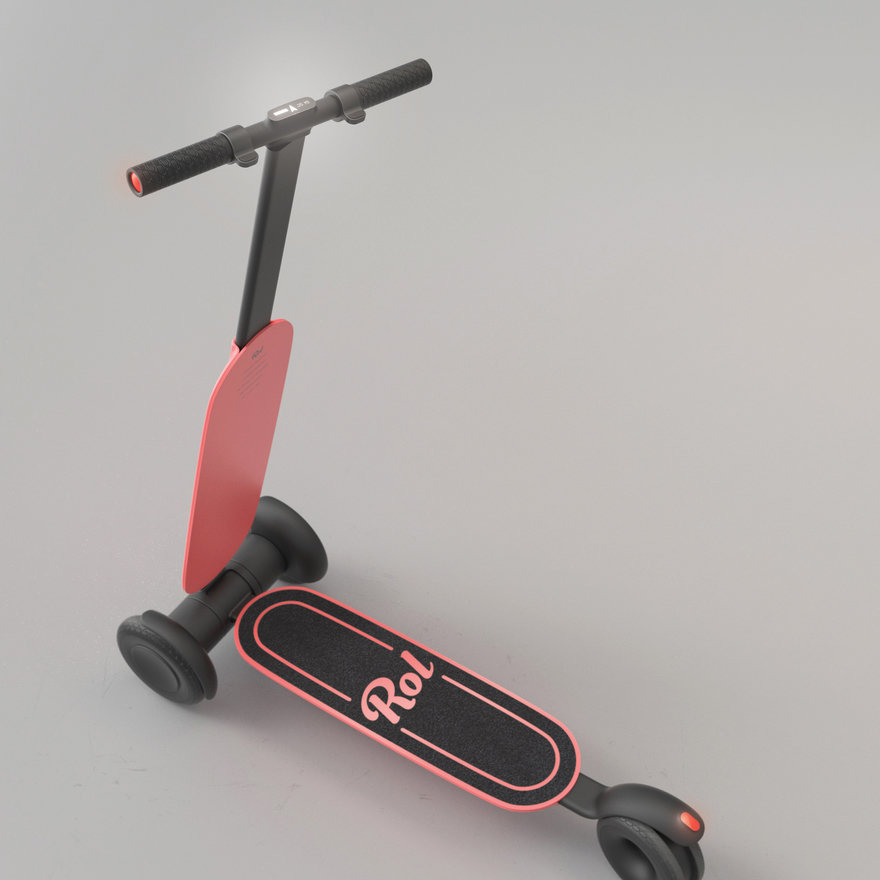
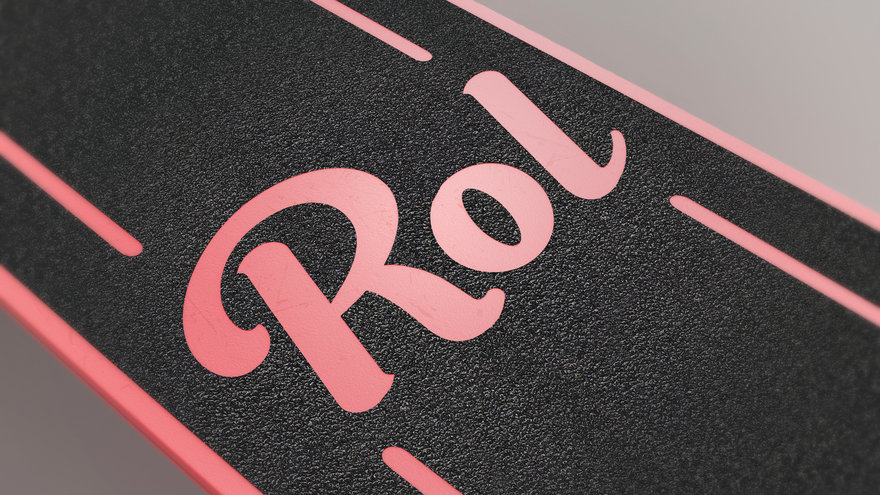
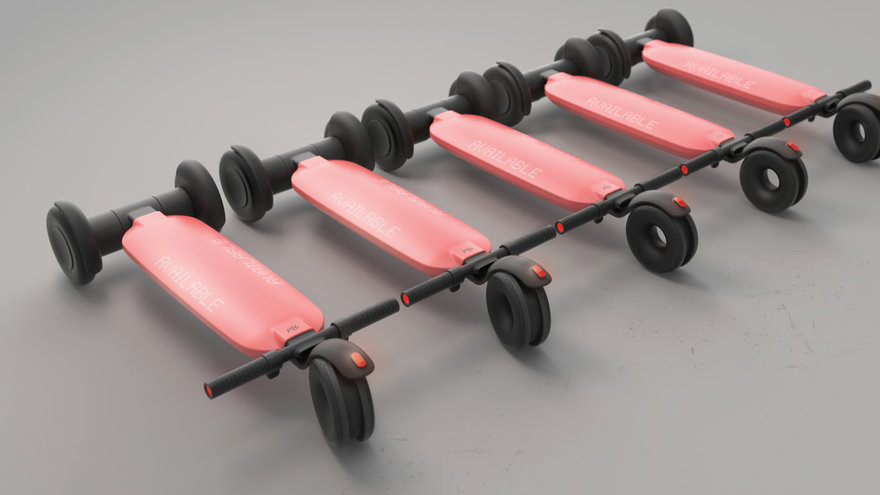
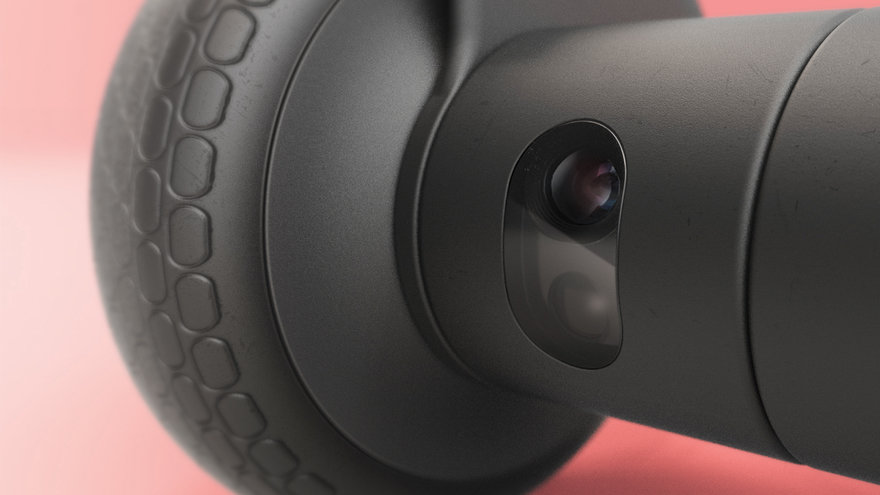
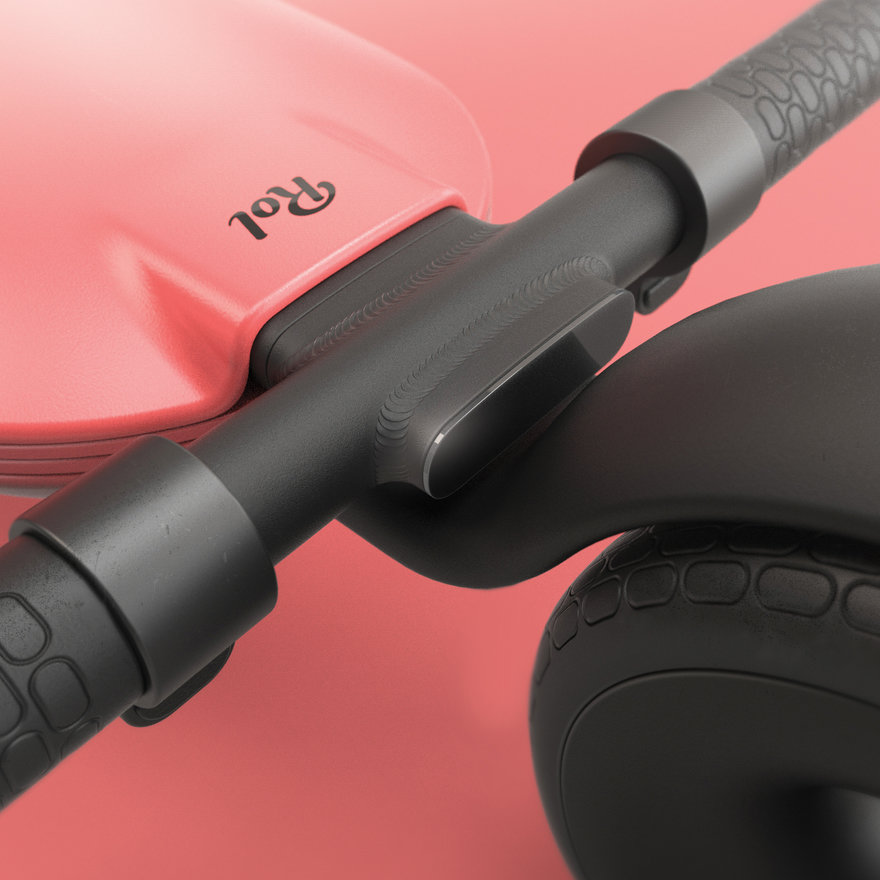
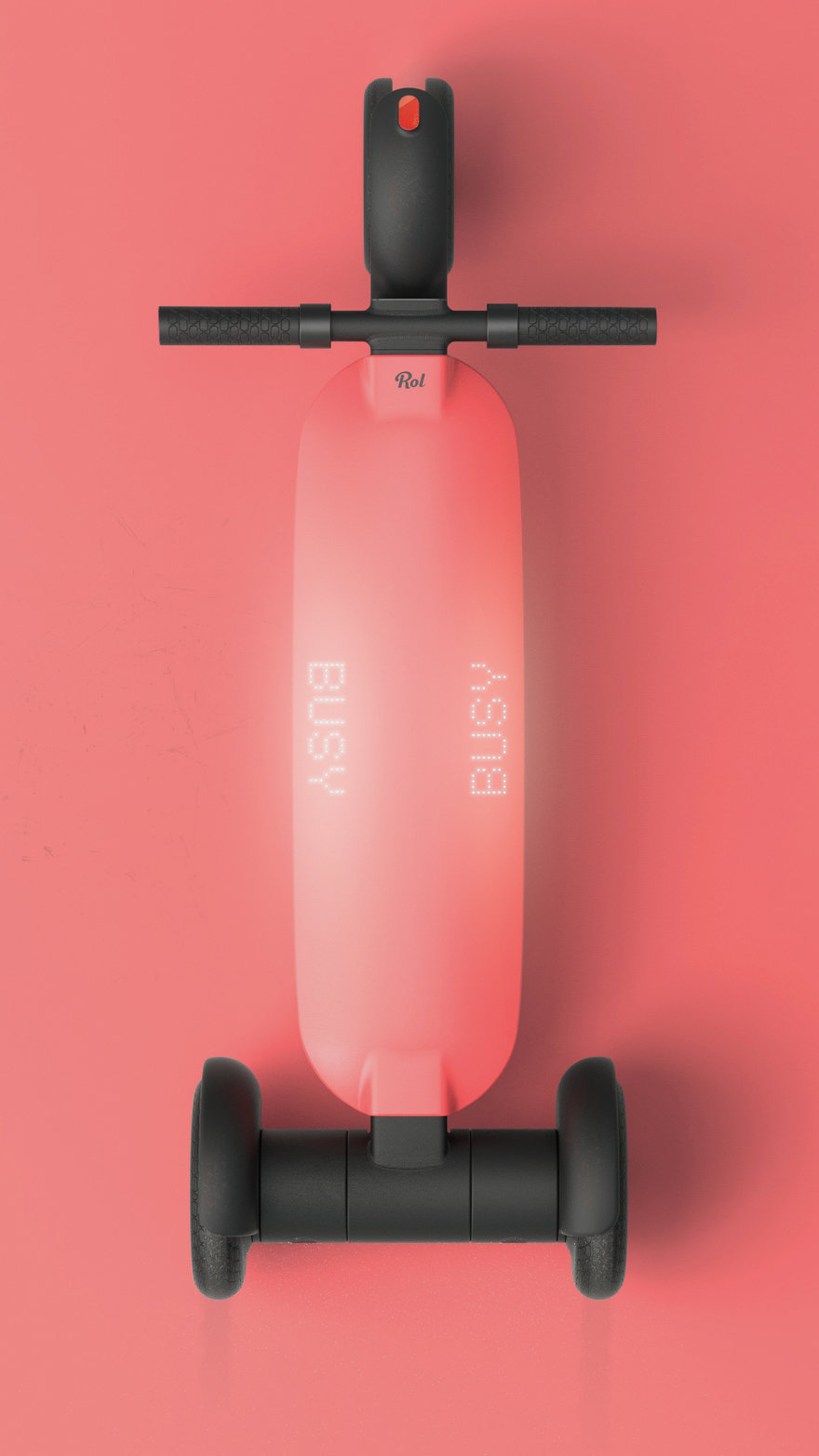
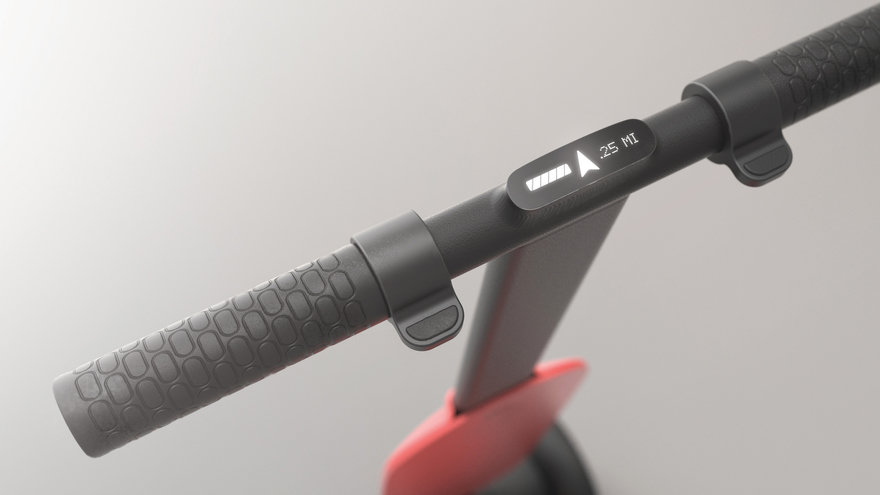
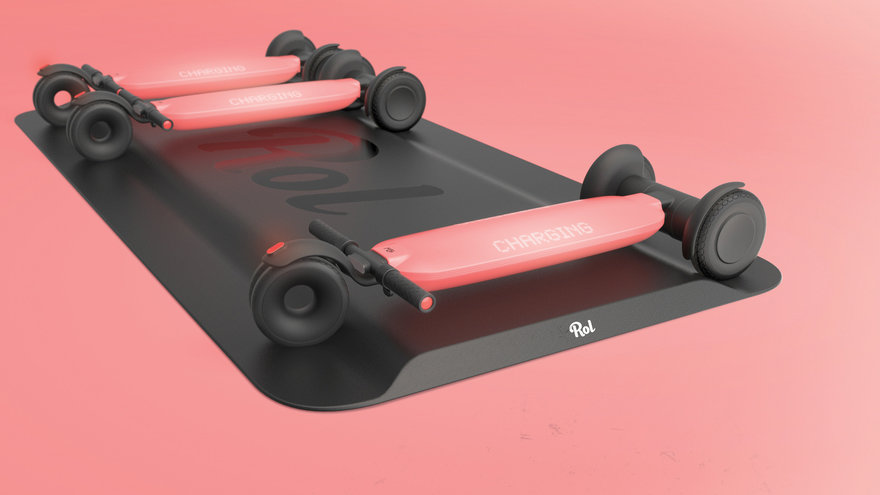
Design Job: Get Your Gear On! - Orvis is Seeking a Designer in Vermont!
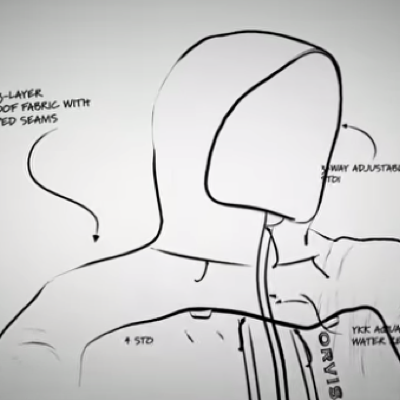
For more than 160 years the Orvis name has stood for a passion for the outdoors and customer satisfaction. Orvis is seeking a Designer for Technical Outdoor Apparel to join our team and ensure flawless execution of product and design vision from concept through completion by creating and executing compelling design concepts
View the full design job hereDesign Job: Get Your Portfolio Ready—Ammunition is Seeking an Industrial Design Intern in San Francisco, CA
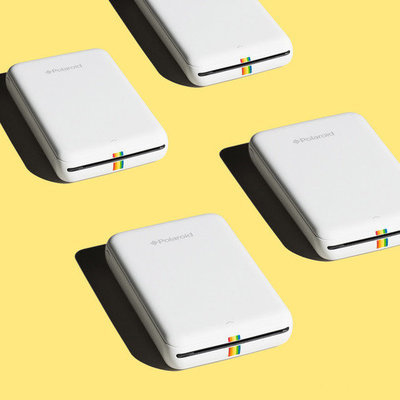
Ammunition is an international design group providing services in product design, brand strategy and identity, UX design, graphic design, and packaging. While Ammunition’s strengths are diverse across design disciplines, our real expertise is to redefine markets by using design to create new business territory, and to communicate and connect with
View the full design job hereReader Submitted: An Organizer Designed for Business Travel that Keeps Clothes Wrinkle-Free and Electronics Safe
Do you ever wish for a business trip where you don't have to worry about the condition of your shirts and the existence of a proper hotel iron? IAMRUNBOX initially developed their garment bags as a solution for commuters to keep their shirts wrinkle free on the go. Along the way, they realized how the simple and optimal way of packing made it ideal for business travelers too. For three years the garment bags have been tested and loved by active people all over the world. Now it's time to give it a little upgrade.
IAMRUNBOX is now launching the Origami Organizer. Specially designed for travelers who want to look their best wherever they go. These packing organizers keep your shirts neat, clean and wrinkle-free and look smart when you arrive with the lightweight hard shell garment bag.
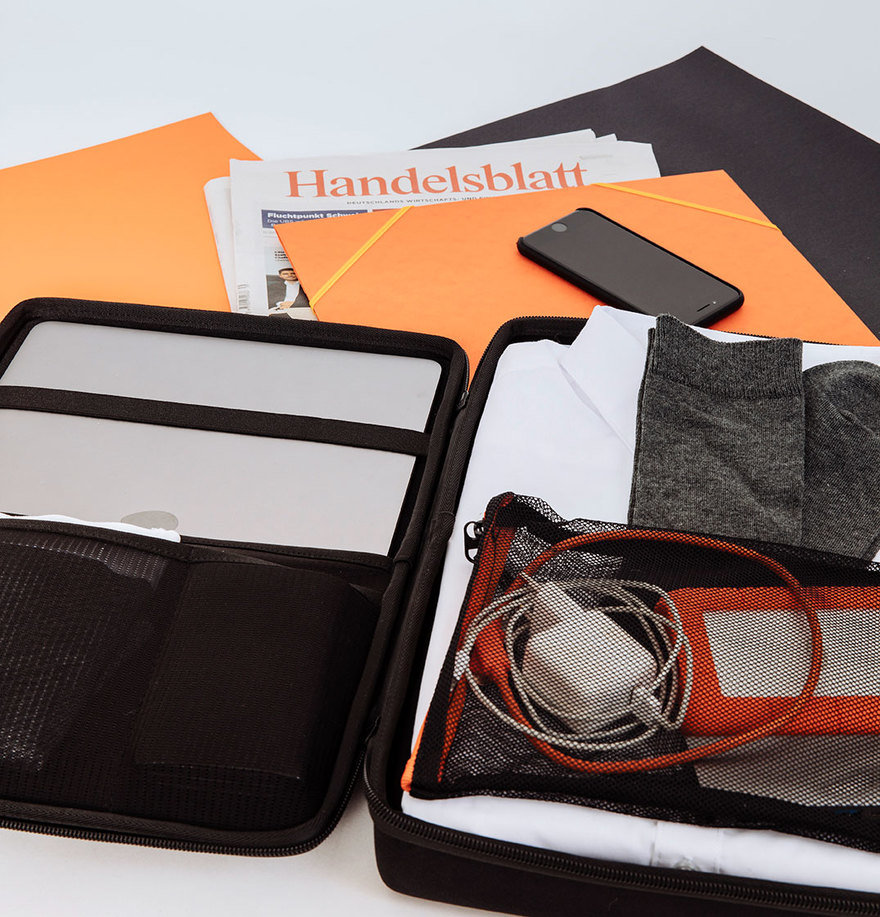
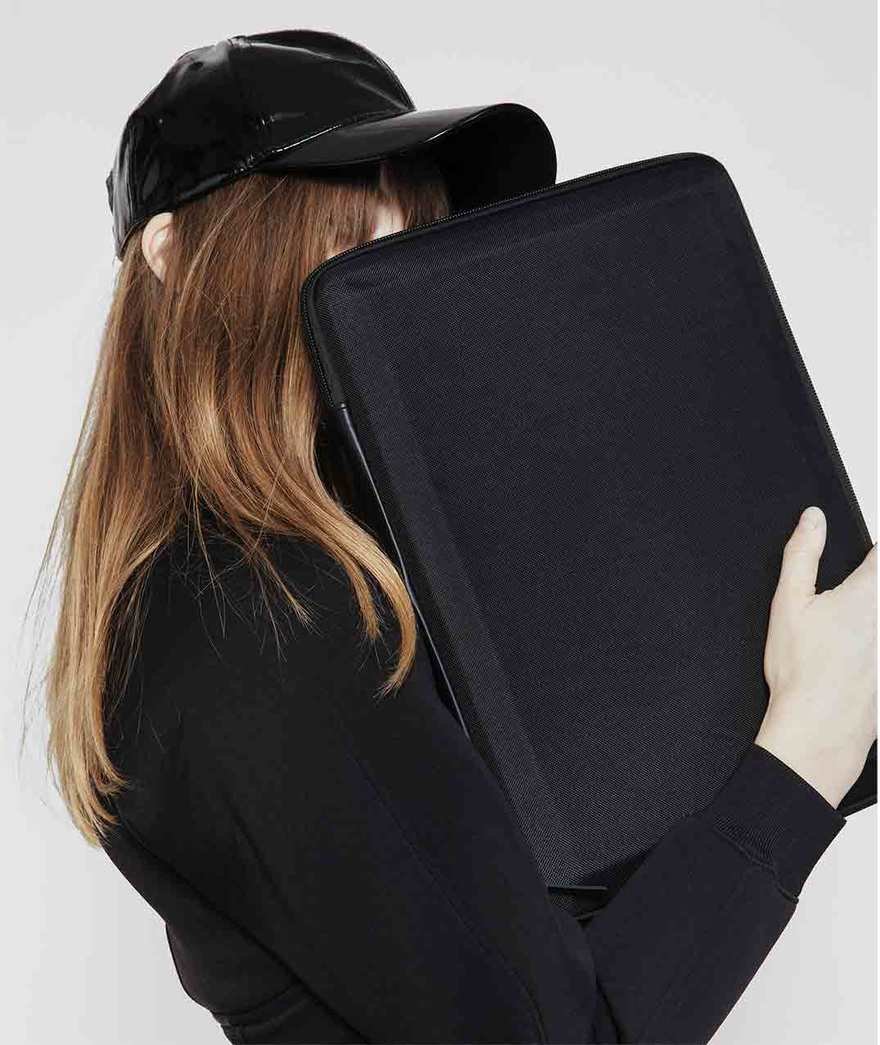
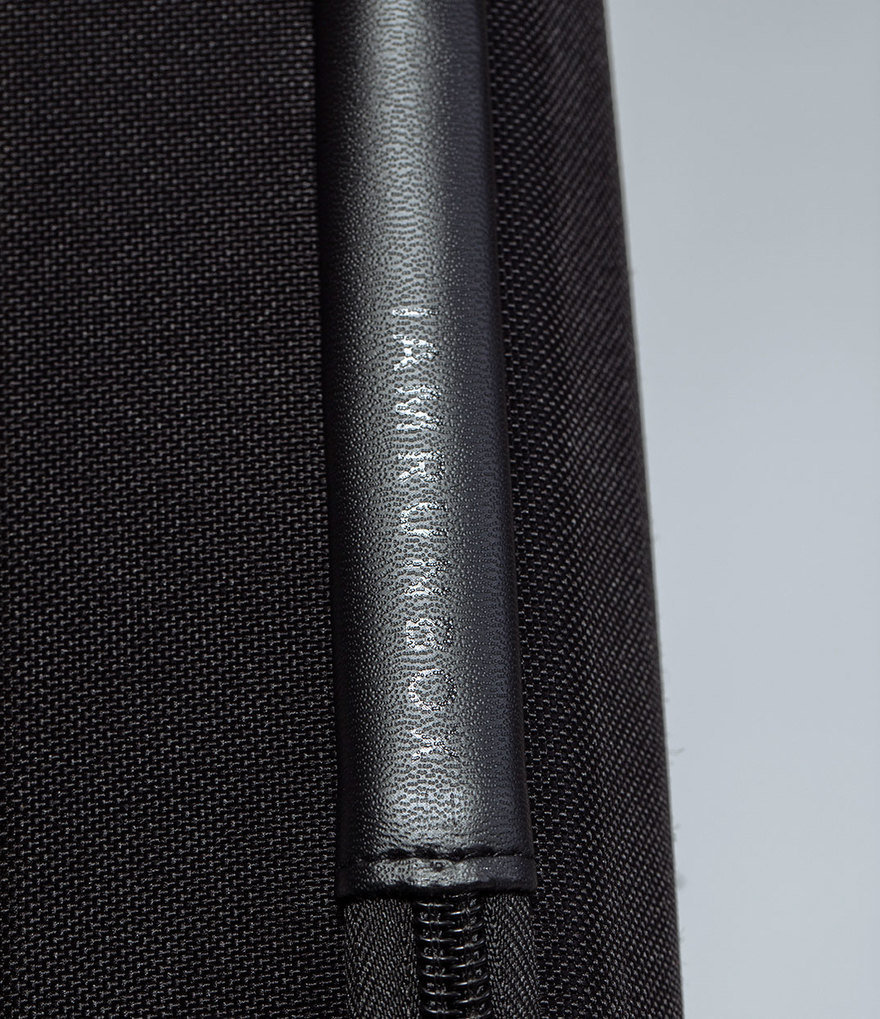
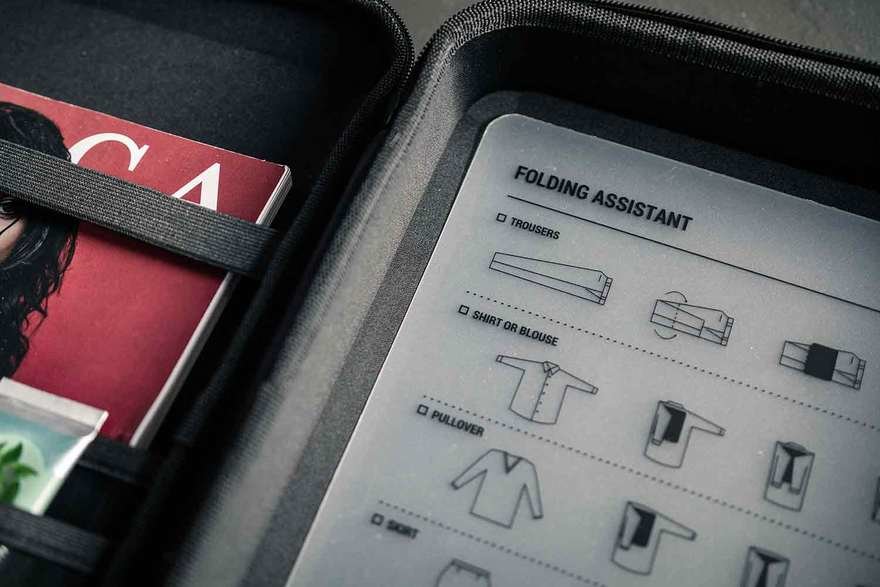
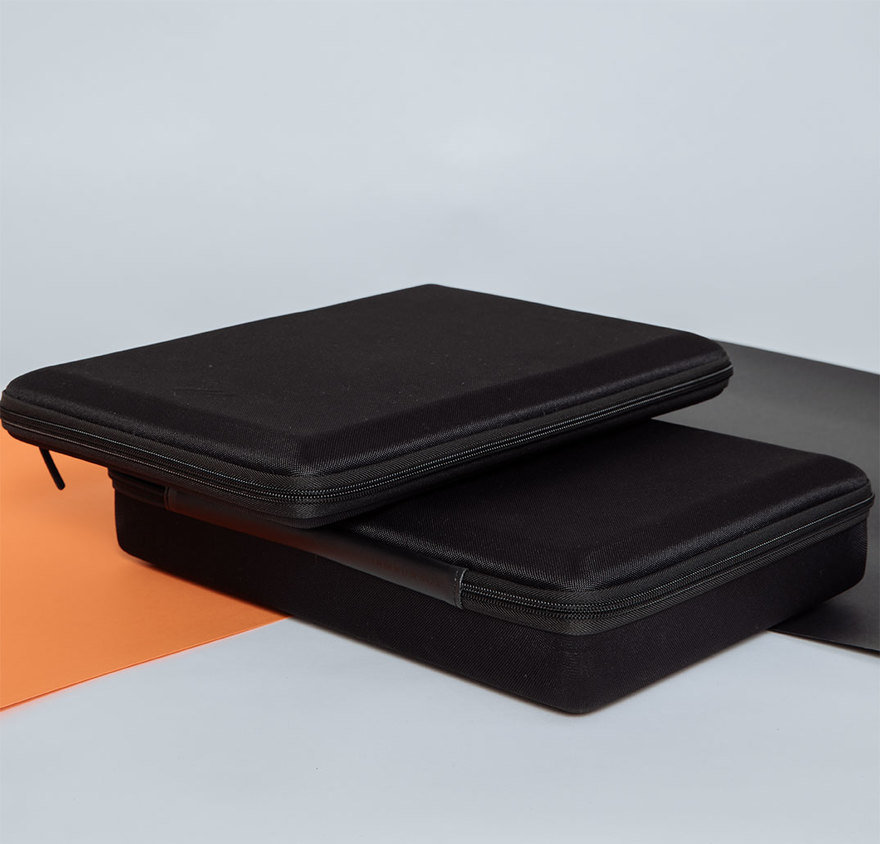
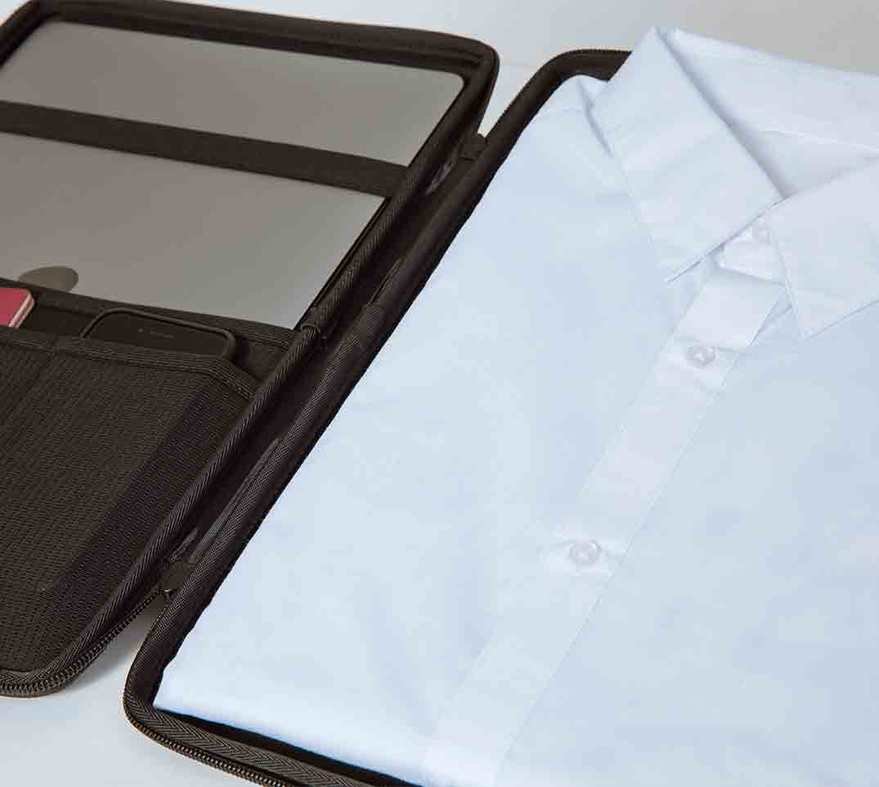
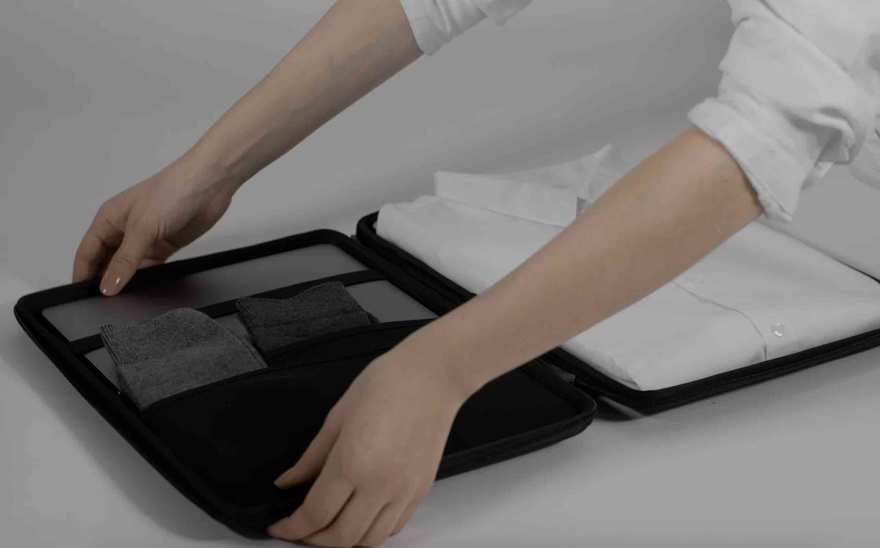
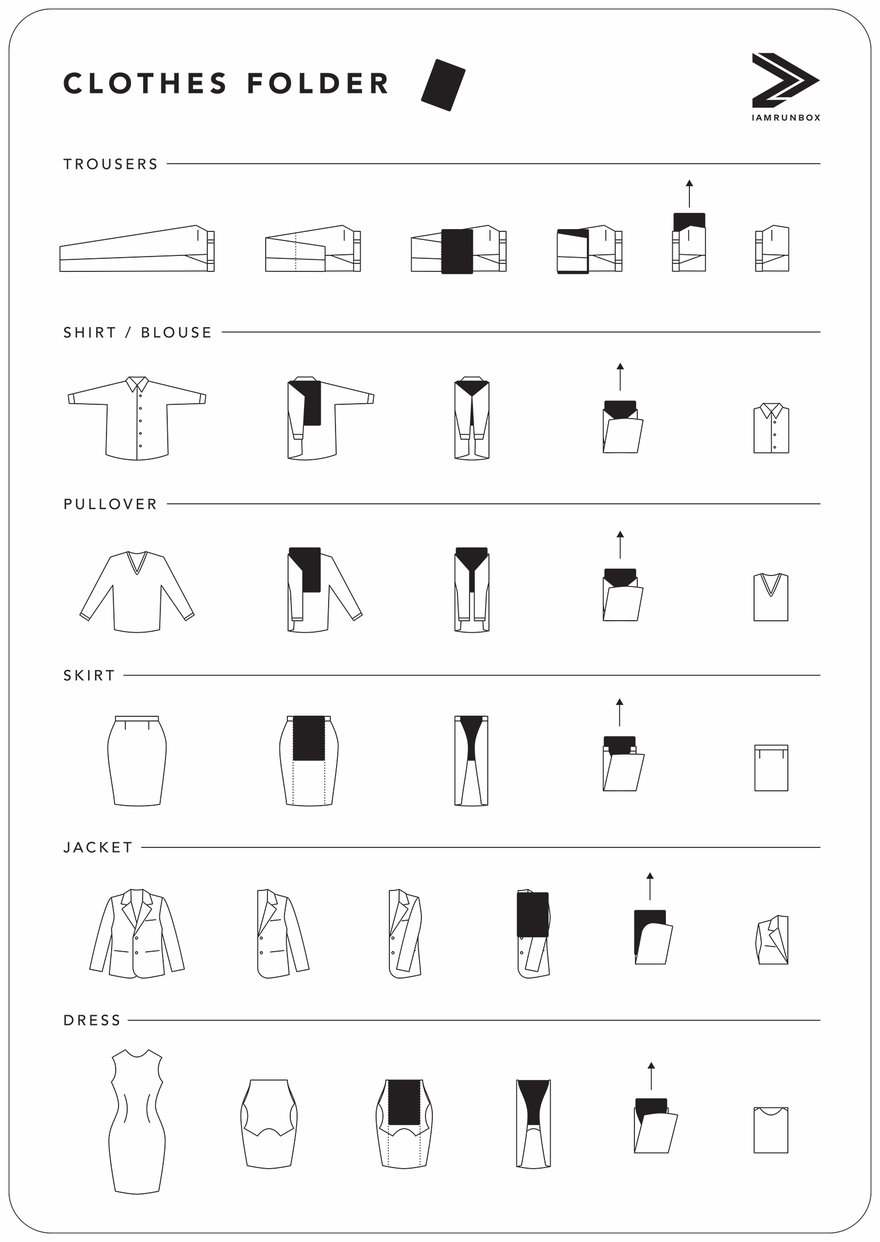
The 2019 Milan Design Week Shows that Demonstrated a New Direction for the Industry
There was something new in the air at this year's Milan Design Week festivities. Was it that there was just so much more to see? Was it the grandiosity of the installations, between retail giants at Salone in Rho Fiera to the previously more underground events such as Ventura Centrale and showroom events? We're still trying to put our finger on it.
What was made abundantly clear is that Salone is no longer just a furniture fair; it's a global event that reigns in the most obscure of studios to tech giants like Google.
What always tends to surprise us about Salone is that despite it's inherently commercial nature and new tech-giant presence, it still manages to show us a number of experimental exhibitions that speak to the wonder of design and not just to commercial value. Despite it's much larger scale in the year 2019, Milan Design Week managed to provide a number of sights that dropped jaws while also engaging a sense of responsibility in the design world, asking the community for more than just a collection of nice chairs. Included here is a selection of just a few of our favorite exhibitions and projects that we experienced during this year's design week.

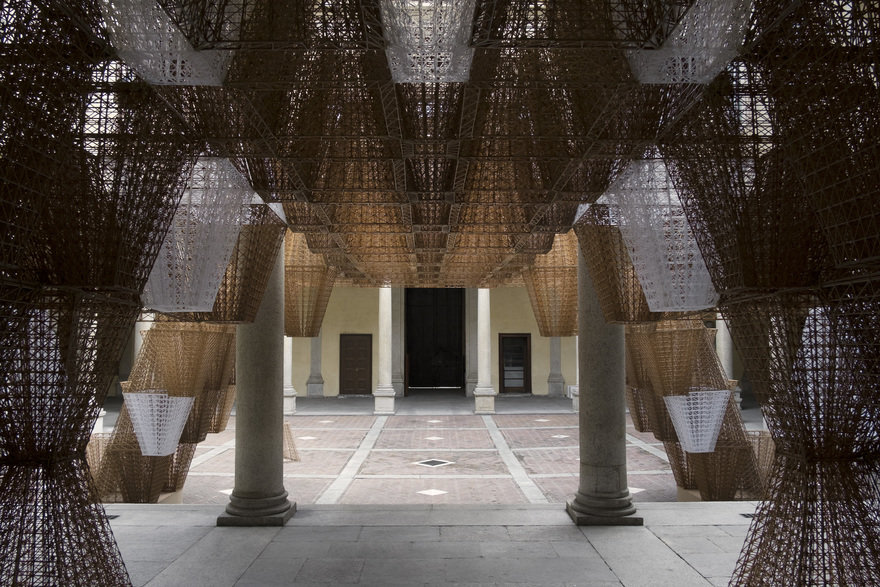
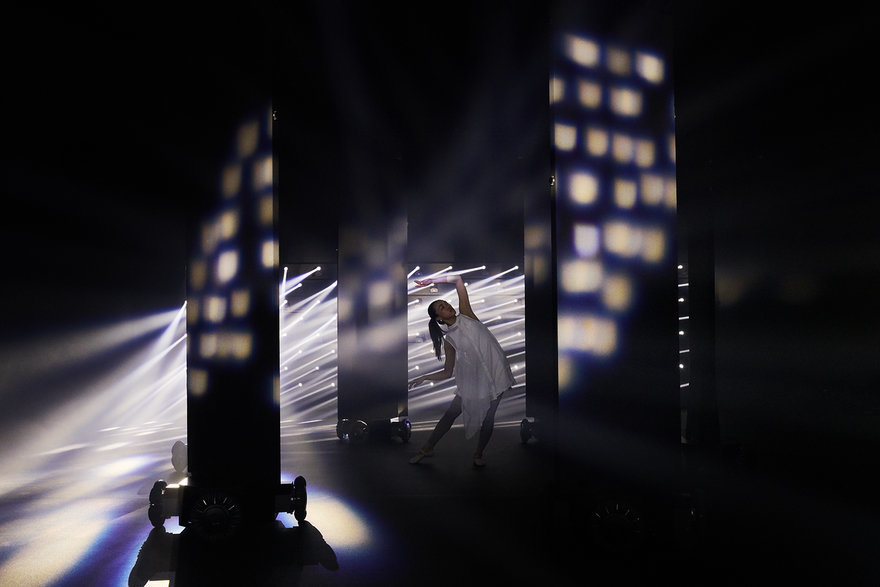
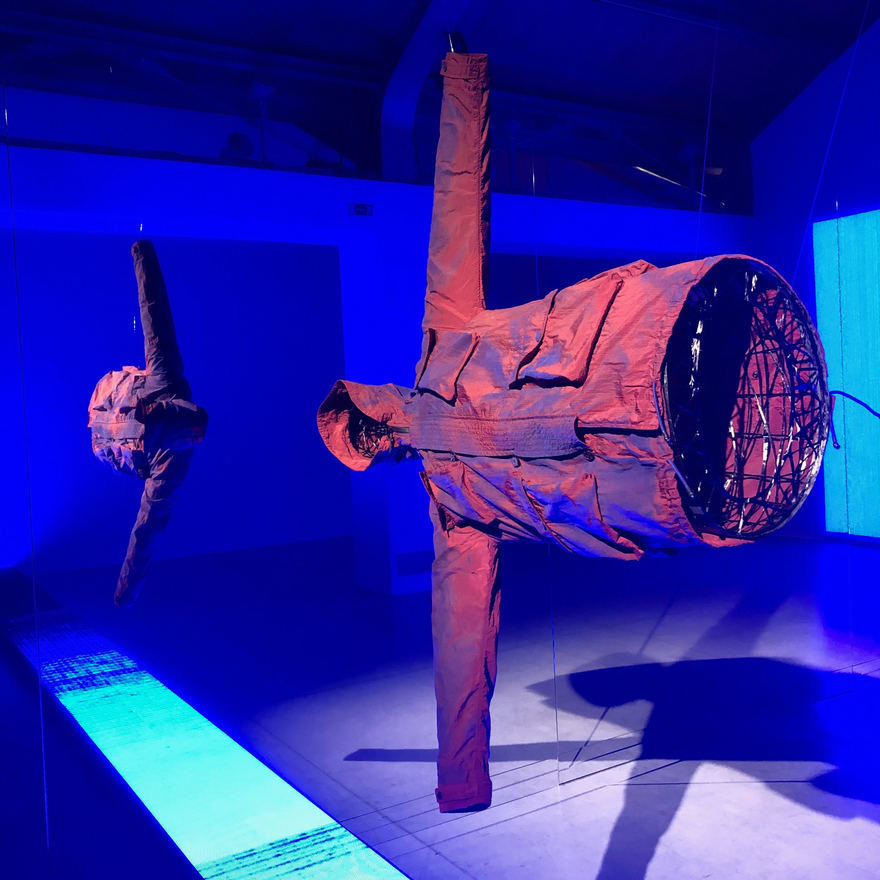
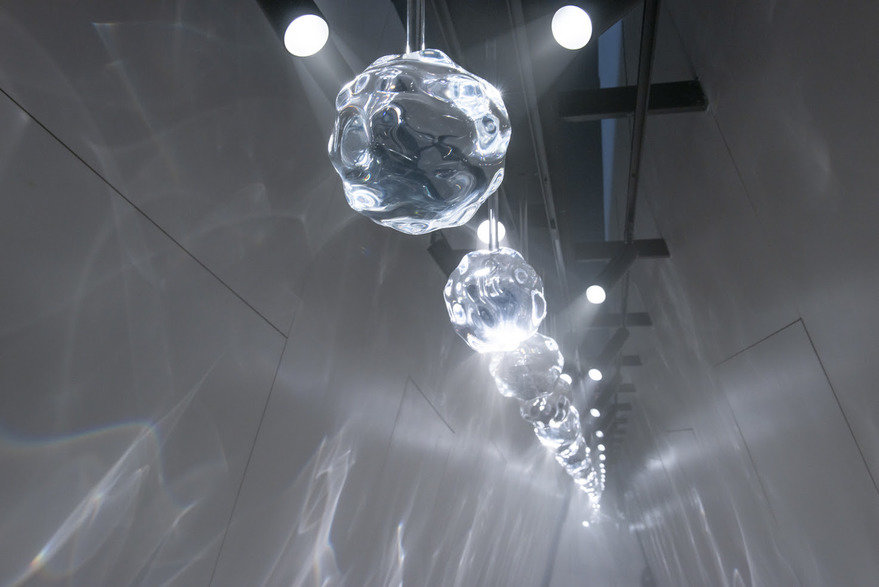
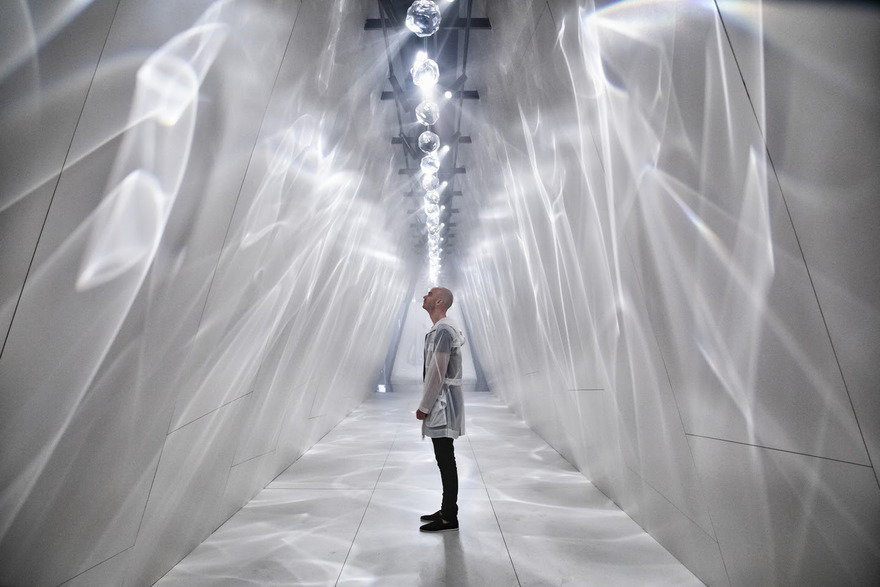
Design Job: Turn Up the Volume: Bose is Seeking a UX Creative Lead in Framingham, MA
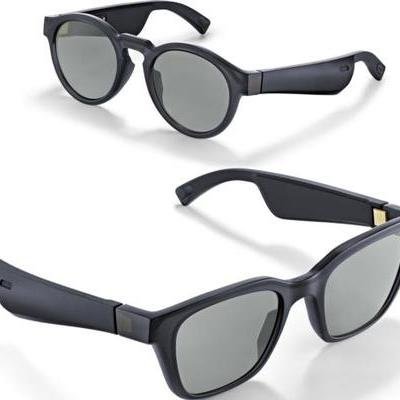
We’re looking for a passionate Creative Lead to join our User Experience team and focus on defining compelling hardware product experiences in our Consumer Electronics Division. Someone who’s excited to bring concepts from advanced development to fruition across our various physical product forms. Someone who has a desire to drive
View the full design job hereReader Submitted: Nook's Design Elevates the Classic Indoor Playground
Nook, a new children's play and learning space in Ballston, VA, reimagines the "family-friendly" destination as a curated, gallery-like experience, filled with thoughtfully designed furniture and multi-sensory installations. No rainbows needed.
This is the third venue to open for the nascent modern family brand, and the most ambitious design and programming effort to date. The project was designed by Mickus Projects, who also fabricated and installed several of feature millwork pieces.
Much of the retail world is defined by how fast they can move: on move-in, on building out a store, on moving merchandise, on shipping goods to you overnight. For Nook we took the opposite approach. We took things slow, spending nearly two years on programming, research, design, iterations, prototyping, fabricating, assembling, installing and styling. The amount of attention we put into every detail is meant to translate into the quality and intention that parents will have with their kids when they come to experience Nook.
We have invested heavily in the process, labor, research and design, resulting in something so beautiful and minimal, wrapping around you and your child. We like to think of it as small-batch design, or single-origin design...a space designed with play in mind.
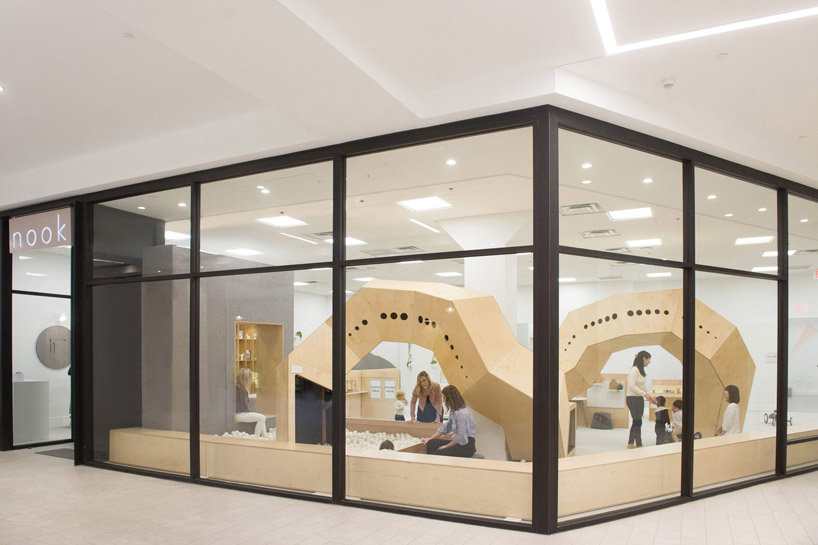
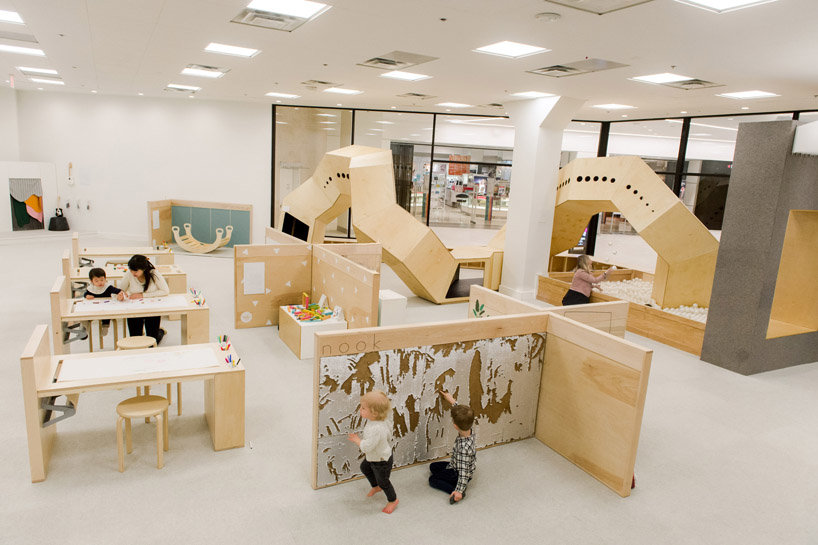
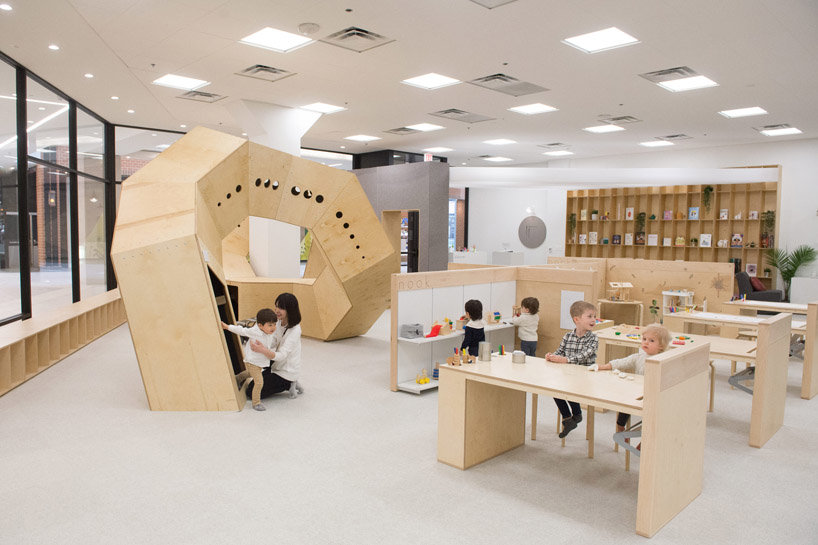
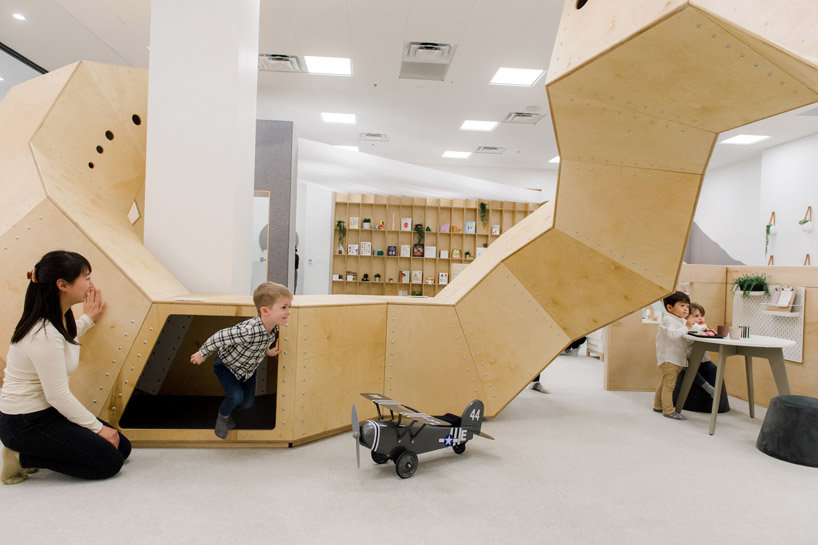
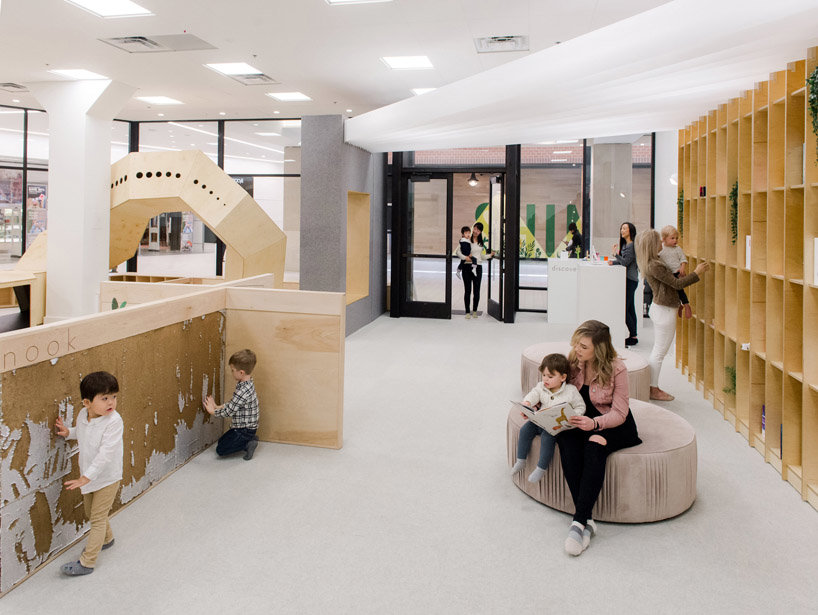
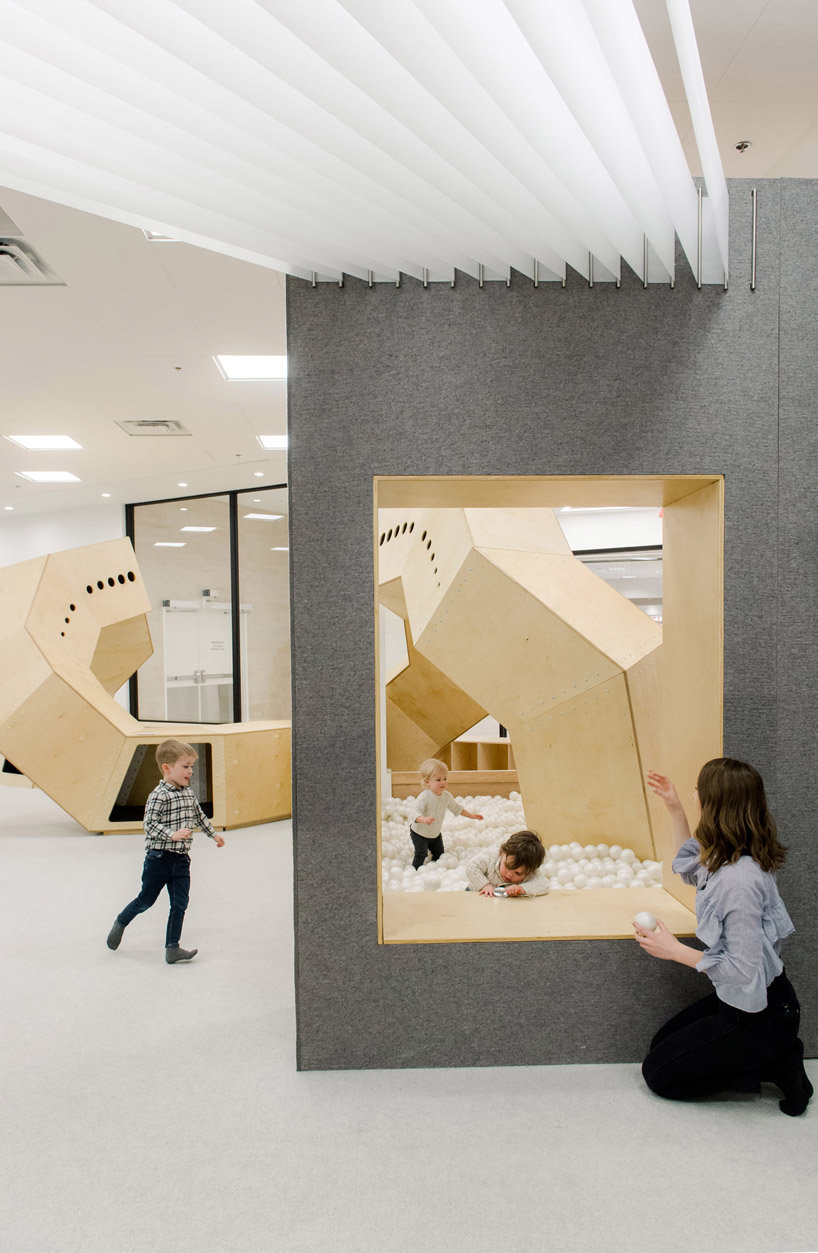
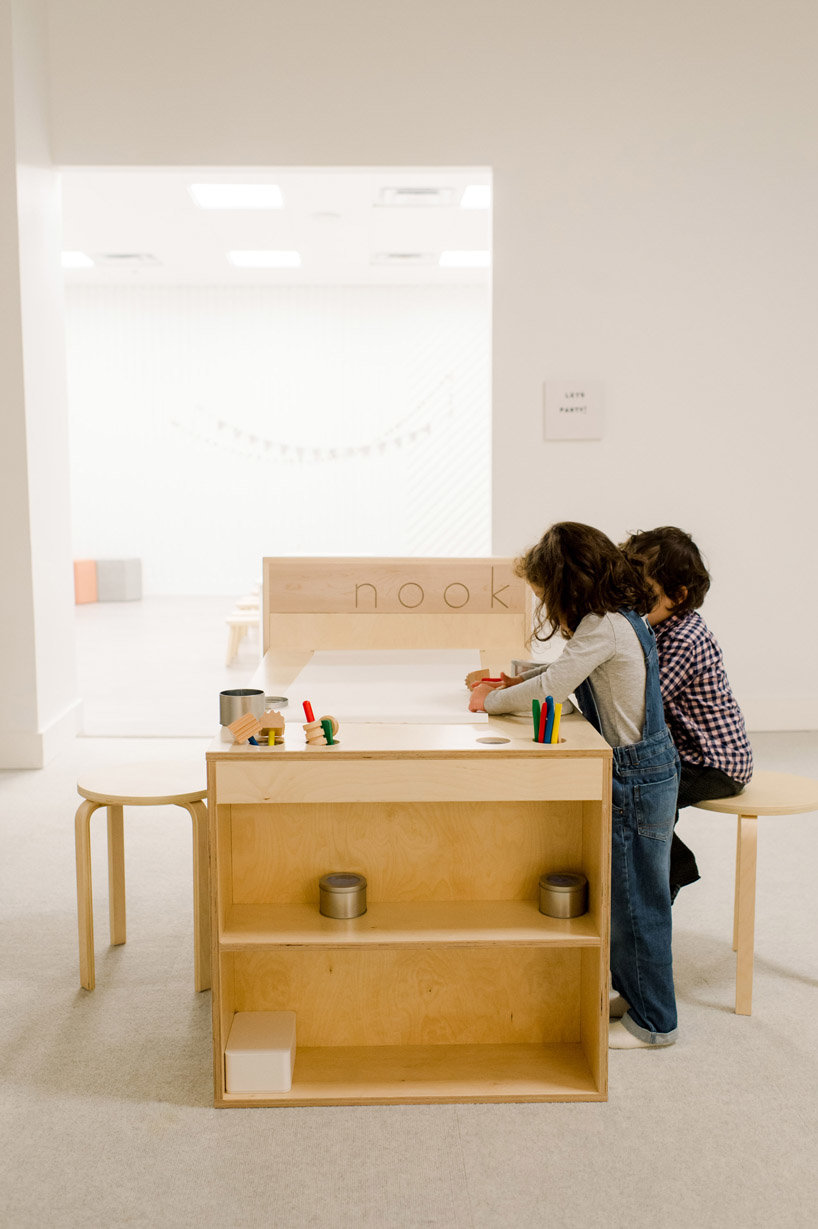
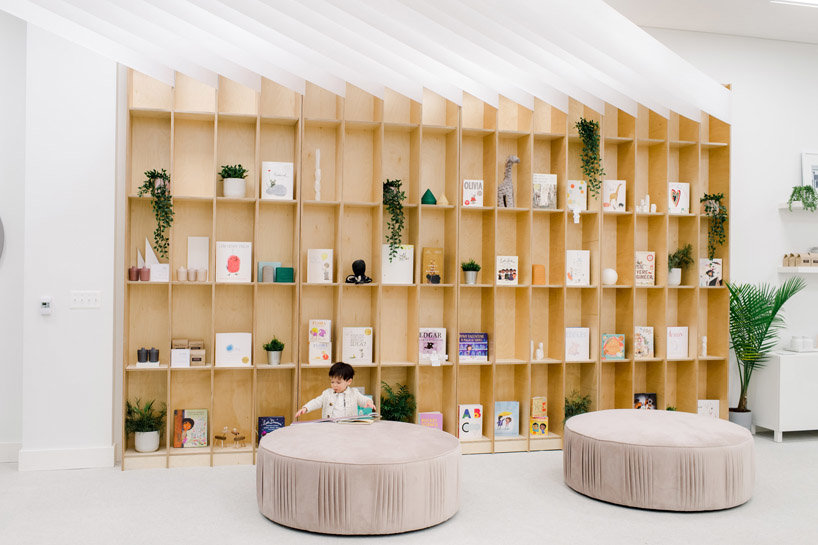
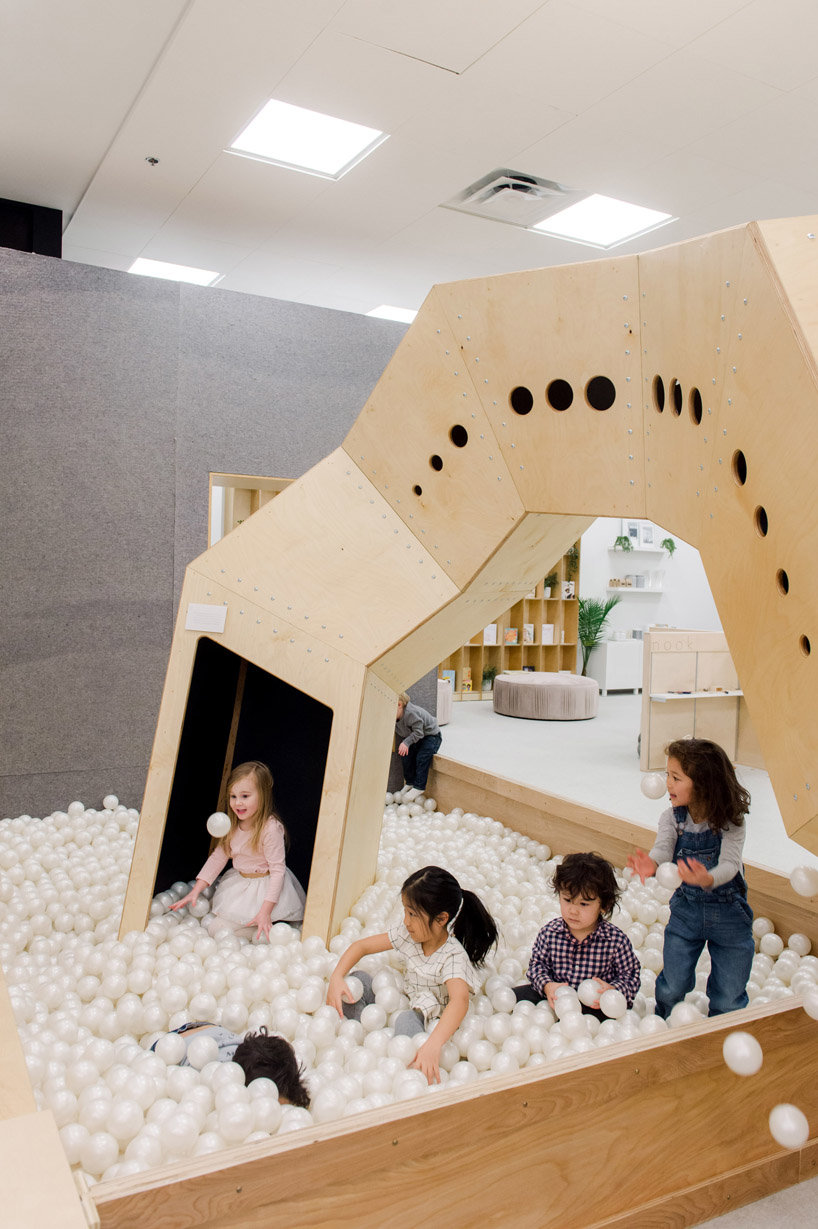
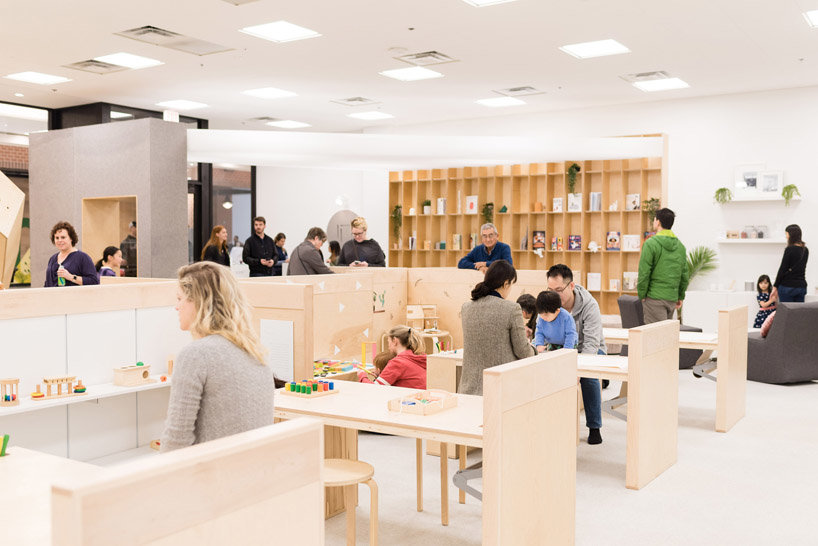
5 Milan Design Week Trends Designers Should Actually Care About
Milan Design Week came to a close this past Sunday, and after a week of visiting installations, interviewing designers and experiencing extreme visual stimulation, we're finally able to take a moment to ruminate over and make sense of what we experienced. While Salone has traditionally been about furniture and homeware design, we noticed a clear shift in interest towards experimenting with technology, understanding the designer's responsibility when it comes to protecting our planet and creating moments of experience around classic furniture. Below is a breakdown of five distinct trends we noticed during our trip, including examples of projects that illustrate a shift in focus for the design industry as a whole:
Imagining a Seamless Future Between Design and Tech
Large companies and independent designers alike explored ways in which tech has the potential to infiltrate our lives in more productive ways than just an AI relentlessly commanding us to stand up and sit down.
Google's A Space for Being TKTK
On the corporate scale, Google imagined a future where tech interprets the environments we desire based on our physical reactions to various spaces and products. Visitors to A Space for Being wandered through a series three rooms, each designed with different furniture, books, textures, lighting and even scents. While interacting with each room as they pleased, a screen-less wearable band silently collected the visitor's data based on subtle reactions, like skin temperature and heart rate. At the end of the experience, the bands were collected and the data interpreted, revealing which of the three spaces the algorithm felt you were most at ease in. The point was less about wearables and more about how this type of tech could have an influence on the design process at all scales, whether it be conducting user research before designing a new chair or even redecorating your own home based on what makes you most comfortable.
Raising Robotic Natives by Phillip Schmitt, seen at Broken Nature
The Triennale di Milano's Broken Nature exhibition examined the relationship between tech and design at an even more future-gazing level, featuring individual projects that look toward the future of human interactions with technology. Raising Robotic Natives by Phillip Schmitt is a designed system of robots, books and soft goods meant to raise the next generation with robots similar to how Gen Z was raised with technology. After being socialized with robots from an early age, "robotic natives" would have a completely different outlook on the importance of and place for robots in everyday life, thus creating potential for new, unimagined developments and interactions between humans and tech.
The result of such examples demonstrated a future that not only distances technology from the cold, distant, sci-fi cliches of yesterday, instead showing how tech can be used as a way to better understand ourselves.
"Handcrafted" by Technology
This year, we noticed less of a focus on handmade design and more of an excitement around the new possibilities surrounding generative design and machine-made processes—especially when it came to machine-made furniture that appeared to be handmade. Perhaps it's because people have stopped associating luxury furniture with handmade items or because companies want to keep churning out as many products as possible—either way, tech appears to be the future of the luxury furniture industry in a big way.
Autodesk x Philippe Starck x Kartell A.I chair
Autodesk, Kartell and Philippe Starck unveiled a prime example of generative design with their A.I chair. "Kartell, Autodesk and I asked artificial intelligence a question," said Starck. "Artificial intelligence, do you know how we can rest our bodies using the least amount of material?" The result is a fluid chair co-designed by human and artificial intelligence through literal conversation. Starck noted a few learning points along the way, including the software's need to learn terms and processes as it worked, but the project shows potential for a new design process, one in which humans and technology are able to collaborate in a surprising new way.
Maruni Hiroshima Chiar
You might recognize Maruni's Hiroshima chair—that's because it's not new. Instead of focusing solely on new product for this year's Salone del Mobile, the Japanese furniture brand decided to highlight a chair that's been on the market since 2008. The chair itself is timeless—if you were unaware of Maruni you'd easily think it were a new piece at the fair. But what sets it apart from many chairs at Salone is that while the shape and wood material appear to be easy to work with by hand, it's actually impossible to make by hand and requires the use of special robots to manufacture. This also decreases manufacturing time, which can't be a bad thing for Maruni.
Responsible Design
Many designers during this Milan Design Week examined sustainability with a wider scope than materials explorations, examining entire product cycles that we need to either break or nurture for the betterment of our planet.
Freitag's Uninfluencer installation
Freitag's "Uninfluencer" installation at Ventura Centrale focused on the individual, holding visitors accountable for their own 'design sins'. Mimicking the Catholic tradition of atoning for your sins, "Uninfluencer" led the visitor through a series of tasks, prompting each sinner to recognize their wrongdoings, confess in a design confessional and ultimately ask for forgiveness. Whether struggling with an unhealthy Amazon Prime addiction or past designs that harm the environment, designers and consumers were encouraged to forgive themselves and take actionable steps towards improving their habits in the future.
Fairphone 2 at Broken Nature
We also noticed a few projects that focused on repairs as a means of sustainability and longevity for a specific product. Fairphone 2 is a modular cellphone designed to be assembled, disassembled and repaired as needed. The phone aims to address the ethical implications of the 'designed to break' model the phone industry follows today, in addition to impossible working conditions, unlawfully minded materials and more. Fairphone 2 is currently on the market today and is on display at Broken Nature in Milan.
Still Running by Marta Sternberg
Repairs were also on students' minds this year—Still Running by Royal College of Art student Marta Sternberg is a redesign of the classic iron that can be disassembled, repaired and then reassembled. The project rethinks home appliances that are often considered deemed disposable as durable objects that can be passed down from one generation to the next.
Confusing Corporate Presence
Upon arriving in Milan, we noticed something big that we hadn't experienced at Milan Design Week in such high quantity before: large corporations, such as Yamaha and Sony started infiltrating the city with installations aimed towards navigating the future of design and tech. Even Juul had a booth at Ventura Futures.
On one hand, the presence of industry giants in a fair environment traditionally meant for furniture and conceptual design ideas speaks to the ever-growing importance of design in the public and private spheres of business and commerce, but it does leave us with questions: Are these companies using Milan Design Week as a way to connect with the design community? Are they using their power to explore design solutions to the world's problems? Or is Salone evolving into an effective way for companies to spend their marketing budget? Only time and the next few design weeks will show how this will affect the shape of Milan Design Week and the industry as a whole.
Sony's Affinity in Autonomy installation
Sony's Affinity in Autonomy installation hinted at building an emotional connection between humans and robots in a vague way. Visitors were led through a series of five interactions, all of which touched on different roles AI plays in the design process.
The Lexus Design Award Pavilion
Lexus has been unveiling their Lexus Design Award winner during Milan Design Week for years and has found a sweet spot between marketing and connecting with the design community. This year, half of their pavilion was dedicated to showing the work of the Lexus Design Award finalists (an awards program that helps fund the design research of up and coming designers), and the other half was dedicated to a light and robot installation that showed off some of the car company's latest innovations.
Instagram vs. Anti-Instagram Experiences
When an entire city is taken over by designers in 2019, you better believe Instagrammable moments are tucked away in every grand Milanese palace. While we do mourn the days when things were less about capturing phone content and more about experiencing moments off-screen, we are happy to say that the graphic installations and colorful spaces seen at Milan Design Week far surpassed "Instagram museums" like the Ice Cream Museum and Rosé Mansion here in NYC.
Vitra's booth at Salone del Mobile
We just talked a bit about corporate presence, which definitely had something to do with the surge in social media marketing throughout Milan (hello money to blow). But we also noticed photo-worthy moments popping up at Salone del Mobile, which typically maintains more of a trade show vibe. Companies definitely went bigger and bolder with their booth displays, creating full blown installations meant to be photographed and shared. An apparent example is Vitra, who combined their furniture and homewares with art pieces to create four different environments, representative of four different personalities.
Benjamin Hubert x Cosentino's Raytrace Installation
On the other end of the mobile content spectrum, there were designers and brands who made a conscious effort to encourage people to put their phones away and live in the moment. Google's A Space for Being installation, which we mentioned above, didn't allow any mobile phone use in the space, and Benjamin Hubert and Cosentino's Raytrace installation purposefully used massive blank shapes, dark lighting and materials like Dekton that are difficult to photograph using a phone.
Design Job: TEAGUE is Seeking a Communication Design Director in Everett, WA
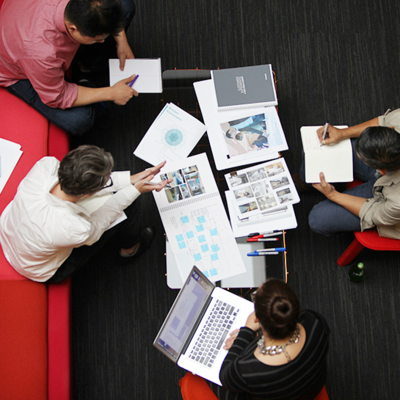
The Communication Design Manager is responsible for driving exceptional graphic design work in collaboration with a world-class design team. This position oversees and contributes to work across a spectrum of projects, including branding, signage, environmental graphics, video, and print. S/he leads the team in developing new opportunities with clients and
View the full design job hereIs Arthur Mamou-Mani's COS Installation in Milan a Nod to the Future of Architecture?
For eight years, fashion brand COS has used the occasion of Salone del Mobile to flex a more conceptual creative muscle, curating memorable experiences such as Studio Swine's 2017 smoke bubble-filled installation and an all-white ethereal, escape dreamt up by Snarkitecture in 2015.
COS Creative Director Karin Gustafsson (left) and architect Arthur Mamou-Mani (right)
This year, they returned to Milan in collaboration with London-based architect Arthur Mamou-Mani to create Conifera, a structure that doesn't just speak to creativity, but also to conservation and innovation. Housed in Palazzo Isimbardi—a building that dates back to the 16th century— the installation is built to figuratively bring you from the old world into the new. The latticed, 3D-printed architectural structure that wraps around the front and back of the palazzo is not only almost fully recyclable, it also currently stands as the largest 3D Printed PLA structure in the world.
"I find it exciting that it's still accessible to break records [in 3D printing]," noted Mamou-Mani, "it's really exciting to know that technology is going at such a speed that enables really interesting environmental designs". Mamou-Mani's motivation, however, was not just about record-breaking, but also discovering how 3D printing might just be able to improve on the physics of architecture. The Conifera installation is constructed out of about 2 million structural elements, and built using a custom algorithm that promises the most minimal amount of material that could take the maximum amount of tension. "The project is interesting in that it's minimizing the amount of materials to a point that it's almost a [structural and weight equivalent to] foam."
"I find this idea exciting, that architecture can not necessarily be finite, but it can kind of undo itself."
Only having a two month window to print the installation presented the team with another challenge to overcome: creating something structurally sound that can also be printed absurdly fast. When asked how they tackled such a feat, Mamou-Mani added that there are many factors to consider to get it right: "It's quite holistic. It's an understanding of the material behavior, the temperatures, the speed, the elasticity...all these parameters we bring in the computer and then use a tool that allows us to integrate all these things together." The parametric design, partly designed by the algorithm, is what allowed for minimal material with maximum structural quality. A not so easy feat, "but I love mission impossible," said Mamou-Mani.
The pieces were made out of a combination of PLA and wood, making it virtually wasteless (given the right composting conditions)—and this, he hopes, has implications for the future of architecture. "Concrete is responsible for about 8% of [humanity's] carbon footprint. It's the second most used substance after water. And steel has a large footprint as well. So together, construction is the number one factor for our carbon footprint," Mamou-Mani explained. "This needs to change, and I think architects need to know that."
So how does Mamou-Mani imagine the future of architecture? "My dream is to have a giant version of this assemble and disassemble a building according to economic conditions. If it's going well, it grows. If it doesn't go well, it shrinks. I find this idea exciting, that architecture can not necessarily be finite, but it can kind of undo itself. I think that's probably the biggest revolution that could happen to architecture, that it's not necessarily permanent and we can let go of this idea." Perhaps a tall order today, Conifera still proves a solid point of what could be.
Currently Crowdfunding: A Better Screwdriver, a Vertical Garden That Will Actually Fit in Your Space and More
Brought to you by MAKO Design + Invent, North America's leading design firm for taking your product idea from a sketch on a napkin to store shelves. Download Mako's Invention Guide for free here.
Navigating the world of crowdfunding can be overwhelming, to put it lightly. Which projects are worth backing? Where's the filter to weed out the hundreds of useless smart devices? To make the process less frustrating, we scour the various online crowdfunding platforms to put together a weekly roundup of our favorite campaigns for your viewing (and spending!) pleasure. Go ahead, free your disposable income:
By now there are plenty of indoor gardening systems to choose from, but this one sets itself apart with a super small footprint (it'll only take up 2.5 square feet of floor space) and a fully automated hydroponic system so even brown thumbs can enjoy the benefits of gardening.
A spinner wheel on the handle of this upgraded screwdriver system maximizes torque so you can get your projects done with less effort.
Here's a waterproof, lightweight cushion that you can throw on any seat to immediately transform it into an ergonomic one. It's designed to keep your back straight, shoulders up and ensure that your body achieves its natural S-Curve.
Can a lamp remind us of the value of energy? The DINA lamp seeks to do just that—you'll have to insert a coin to get it to work. But this is just a gentle reminder: the amount you put in won't impact how long you can keep the light on. To turn it off, you just pull the wooden nob and the coin will fall into the wooden base, where you can retrieve it at any time.
The Narwal robot mop and vacuum will clean your floors then go to its nifty dock where it will clean itself before it goes back out there and does it again!
Do you need help designing, developing, patenting, manufacturing, and/or selling YOUR product idea? MAKO Design + Invent is a one-stop-shop specifically for inventors / startups / small businesses. Click HERE for a free confidential product consultation.
adidas Unveils Zero Waste Plan, Starting with 100% Recyclable Sneakers
Before we get into the details of adidas' heady new footwear release, let's give it some context: over the past few years, adidas has led three main initiatives—Parley, Futurecraft and Speedfactory. Through a partnership with Parley, adidas' line of footwear and apparel made primarily from recycled ocean plastic signified a shift towards environmental awareness for the brand. Before Parley works with a company to produce product, they require a pledge from the company, essentially stating their actionable plan to implement less plastic into their production process. The Parley initiative paid off for adidas: the collaboration resulted in a product that is in the hands of consumers today, and it positioned adidas as a fast fashion company who at least cared about the environment enough to try.
Then there are Speedfactory and Futurecraft, which both focus more on customization and innovation with industrial processes. "Speedfactories" are actual facilities (the first was in Germany) that focus on streamlining the process of customization and creating unique product based on the individual consumer's needs. Futurecraft is the company's all encompassing label for innovative projects, most notably producing the Futurecraft 4Ds, a runner with a liquid 3D printed midsole designed in partnership with Carbon. The goal with Futurecraft 4D was also customization, as the 3D printing process is able to yield personalized midsoles with specific density placement based on the individual user's need.
Parley, Speedfactory and Futurecraft were kept separate with a little overlap here and there, but adidas just announced a new product and business strategy under the Futurecraft umbrella that appears to combine important elements from all three initiatives.
Futurecraft.loop is an approach to designing shoes that are made to be remade by using only one material (100% reusable TPU) and no glue. The TPU is treated in a variety of ways to create a full shoe, including being spun into yarn, knitted, molded and clean-fused to a BOOST midsole. The process employs the use of SPEEDFACTORY technology, which combines the sustainable effort with the quick manufacturing of special models.
After the shoes are worn to death, they are meant to be returned to adidas where they are washed, ground up into pellets and melted into material to create a new pair of shoes. The process yields zero waste, and no material is ever thrown away.
Instead of releasing yet another sneaker, adidas is releasing an entire system, which we're curious to see put in place—hopefully sometime in 2021. adidas has already proven their ability to innovate in the material space and manufacture customized products at a relatively high speed, so now comes the real challenge: pulling knowledge from their past efforts to implement a true closed loop, zero waste system as part of their business model. Their proposed system also involves empowering consumers to return used shoes to be reused and remade into the next pair. How will this process be communicated and designed? Will consumers care enough to put in the effort of returning old shoes? Only time will tell, but for now 200 testers will have their hands on a beta pair to help adidas run through a simulation of what the future of the company could look like.
Design Job: Clean Up Your Career! Newell Brands is Seeking an Industrial Designer in Huntersville, NC
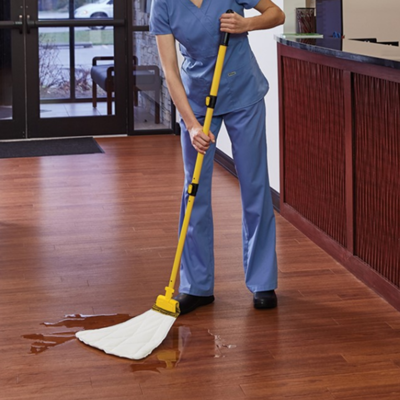
This Industrial Designer will conceptualize and develop new products that improve the lives of our customers. In this role you will be involved in all aspects of Industrial Design. Collaborating closely with cross-functional teams to create customer experiences for the next generation of products.
View the full design job hereClever Tool Design, Bold Entrepreneurship: The Story of the American-Made LogOX
There's a reason that only a tiny proportion of the population successfully launches their own product design. In addition to correctly identifying user needs and getting the design right, you also have to nail the manufacturing, the marketing, the distribution network, the customer service. It takes design skills, patience, research, networking and a whole lot of hard work.
Meet the Roberts family. They're three members of that tiny proportion. We think you can learn a lot by reading their product development story, and how they managed to launch a must-have tool in the outdoor products segment. Their story starts, as many invention stories do, with a disaster.
An (Unexpected) End of a Career
An engineer by training, Jon Roberts was a problem solver. He'd started off in product development labs, and over the years he'd successfully solved enough problems to work his way up to Chief Operating Officer of a multinational industrial manufacturing firm. The hours were long, but life was good. He and his wife Lynne lived the way they wanted to, in a log home nestled on a 13-acre plot in the woods of Vermont.
But one Thursday in June of 2016, Jon ran into a problem with no apparent solution.
He and 17 other key employees were being laid off.
It didn't make any sense to him. Part of his prototyping methodology was to figure out what was working and do more of that, and to identify what wasn't working and get rid of that. And the division Jon headed up was working. "The company was struggling with some of its international divisions," he recalls, "but our U.S. division, under my direction, was doing well."
Nevertheless, the company brass had issued orders "for all divisions to lay off all personnel, at all levels, to achieve a total financial savings." Jon and the 17 others were wiped from the roster on that Thursday. By Friday, his office was empty, his things removed. His nearly 40-year career had been erased in the blink of an eye.
An Age-Old Problem
After recovering from the initial shock, Jon began looking for work. He figured that his skill set and experience--lab work, product development, finances, operations--would be valuable to a variety of companies. But ironically, the years it had taken him to gather that expertise were now working against him.
"I found it was next to impossible to find a job, despite working with head hunters and scouring the internet, looking for opportunities," Roberts remembers. "Age does matter. I had read about the problems people over 55 had trying to find a job. I can now say I was one of them." To keep his chin up, Jon repeated his favorite saying to himself, learned way back when in the lab: "Out of crisis comes opportunity." But he hadn't yet figured out what the opportunity was.
Jon broke the news to his wife of 31 years, Lynne, as they walked their two Boxers along the dirt road leading from their house: He was out of work. There would be no more money coming in. What would happen to them? Could they keep the property, would they have to sell the house? (While any homeowner is attached to their house, this one held special significance--Lynne had served as its general contractor, some 24 years earlier.) Then there was Mia and Callie, the two Boxers on the other end of the leashes; at nine years old and in failing health, Mia had recently racked up $6,000 in vet bills.
"We were already very stressed and overextended on finances," Lynne remembers.
Which made her reaction to Jon's termination all the more unexpected. "I saw it as a Godsend," she says. "Jon was getting up at 5am, driving an hour and a half each way through heavy city traffic, putting in stressful days, managing a large New England facility and five other plants, then coming home around 7:30, eating dinner and going to bed. Rinse and repeat the next day.
"The money was good," Lynne continues, "but our quality of life was not what I wanted for us. I wanted our lives to be more rewarding, independent, and fun."
All fine and good, but if no one would hire Jon, what were they going to do for income? Where was the opportunity hiding behind this crisis?
Back at the house, down in the basement, was Jon's small 12' x 14' workshop. Sitting on the workbench was an oddly-shaped contraption of metal parts. That object was a hobby, a compulsion of Jon's. And it was a money loser.
Birth of an Idea
Well before they'd built their log home, the Robertses had lived in the woods of New England. Local trees were a crucial source of heat during the brutal winters. For decades Jon had carried his Stihl into the woods to fell damaged Maple and Ash trees, then buck them up into 16-inch-long rounds. Those rounds then went onto a trailer for transport or directly onto the log splitter. After drying out in a stack for several seasons, the resultant splits would finally go into the woodstove, where they'd warm the whole family.
In the product development labs where Jon turned his Chemical Engineering degree into a career, he wore a white lab coat, protective goggles and chemical-resistant gloves; out in the woods he wore protective chaps, an orange Husqvarna helmet and suede gloves. But while the uniforms were different, Jon saw harvesting firewood the same way he saw product development, in that he instinctively analyzed the process to see what needed smoothing out.
At step 1, a well-maintained chainsaw did a fine job of felling the trees, and at step 2, bucking them into rounds.
Stock photo of log bucking by Rvannatta at the English Wikipedia, CC BY-SA 3.0
At step 3, the splitter easily cleaved the rounds into firewood. But one glaring issue for Jon was between steps 2 and 3, which was picking the rounds up off of the forest floor, centralizing them, then hoisting each one up to the deck of the wood splitter, about 30 inches off of the ground.
A typical log splitter
"When you fell a 60-foot tree and block it up, you have a lot of 16" pieces--maybe 40 to 45 of them--to process," Jon explains. Some of these pieces might weigh 90 pounds or more. Jon, at 5'11" and 195 pounds, could manage lifting a single round without breaking a sweat; but multiplied by 45, it became far more bending and lifting than he'd like.
In an effort to make the task easier, Jon had gravitated towards using a pulp hook:
A pulp hook
This wicked-looking implement was moderately effective, but rather dangerous. In order for the hook to bite into a log that's lying on the ground, you must swing the tool into the log with considerable force, and your aim must be true. If your attention or your grip slipped, "it could be a really bad start to your day," Jon says. "Everybody talks about driving it into their shin from time to time."
Jon wasn't using the pulp hook because he thought it was the ideal tool for the job; he used it because it was slightly easier than bending over to pick each log up off of the ground. "You drive the pulp hook into the end of the log, and you can start picking up that end, and then you can slip your hand underneath it. So in the overall lifting process, it does make that portion go a bit smoother. You're not having to bend over quite as much."
However, "It's very inefficient," Lynne points out. "The point of the hook falls out a lot." On top of that was the danger: "It made me nervous to watch him use it," she adds.
One tool that didn't make Lynne nervous to see Jon use was a cant hook:
A cant hook
The cant hook is a timeworn and effective design that loggers use to roll logs over during the bucking process. If a log is lying on the forest floor, you cannot cut it all the way through with a chainsaw, or you risk the chainsaw bar getting stuck in the log, as the weight of the log forces the cut to close. (The way I describe this phenomenon to my urban friends: Imagine sitting down on the subway with two heavyset people on either side, and they both fall asleep and lean onto you.) Cutting entirely through the log would also risk the chain touching the dirt, which dulls the teeth instantly, and resharpening in the field is a time-consuming process. So instead the common practice is to cut slices partially through the log, then roll the log over to complete the cuts from the other side, freeing the rounds.
As logs can be quite heavy, the cant hook is designed to use both purchase and leverage to make rolling them over manageable. It engages with a log by means of a tooth that bites into the bark. Opposite the fixed tooth is a hinged, curved arm that terminates in a sharp hook, and once that swings down the tool provides bite on both sides. The user then has enough purchase to roll the log over.
One day Jon was using a cant hook and observing the design of it for the umpteenth time. "I was taking a break, sitting there and looking at it. And thinking 'This works nice, this is a real handy tool.' The way it's designed, it really does grab onto the log and help you roll it over."
The DIY Contraption
For more than 30 years of firewood harvesting, Jon had wished there was a better way than a pulp hook to lift log rounds. And as he was mentally praising the efficacy of the cant hook, he got an idea. He began experimentally using a cant hook to lift log rounds straight upwards, just to see what would happen.
A cant hook is not designed for this purpose and, predictably, failed to do it consistently. "I found that maybe 60% of the time, the log would slip out as you lifted it. Obviously, that kind of failure rate is not acceptable," he says. It would, however, successfully lift a log 40% of the time, and this intrigued Jon. He drew on his product development training to advance the idea: "If you can see that it will do it once, you have to figure out what the key to that is. It was failing 60 times out of 100, but there was 40 times that it was picking it up. So, how do we change this so that you get to 100%?"
Jon observed another problem, which was that the 40% of the time it successfully picked a log up, it was still no good as a means of carrying that log over to the splitter. That's because the handle is a just a straight rod, meaning that under load "it's not balanced at all, and the log it was carrying would tilt towards you. It was not user friendly for, say, walking through the woods with it because the log was swinging in towards your legs."
By tinkering, Jon discovered that solving the second problem magically solved the first. On weekends he was hacking the tool in his basement workshop, analyzing the tilting/unbalancing problem by adding an offset handle to the tool's shaft. This centered the carried log beneath the carrier's hand--and yielded an unforeseen benefit:
"By moving the handle away from the main body, creating this cantilever effect, I immediately found the tool would now use the weight of the log itself to lock the hook into it, holding it in place. Just changing that aspect of the design became a key turning point."
But as often happens in product development, these improvements yielded a new problem: The tool now picked up and held logs so securely that it didn't want to release them. Jon attacked this problem with the same patience, studying the hook to optimize its geometry.
After more tinkering, Jon had something that worked. It was crude-looking, Frankensteined together from parts of an existing cant hook, pieces of metal Jon had bent in a vise, and a hand-shaped wooden doodad that served as a junction for these unlikely parts. But the contraption would firmly grasp logs, then release them as desired with a flick of the wrist.
Jon with an early prototype
That problem solved, Jon began pushing the design further. He developed a removable handle extension that transformed the tool into a proper cant hook; the increased leverage of a longer handle allowed one to convert it from log carrier to log roller.
Current-day production version, cant hook mode
Current-day production version, cant hook mode
Taking it a step further, he then developed a removable T-bar that turned the tool into a timberjack, allowing the user to not only roll a log over, but elevate one end off of the ground in a fixed position.
Current-day production version, T-bar
Current-day production version in Timberjack mode
Current-day production version in Timberjack mode
These innovations tripled the tool's functionality, allowing the one object to take the place of three tools that anyone harvesting firewood might need. He had invented a forestry multi-tool, and it broke down to a compact size, making it easy to carry into the woods.
Jon had developed this iteration in 2014, with no idea that he'd be laid off in two years. It was a DIY aid, a hobby, a compulsion. And he was so pleased with its design that he wanted to create a more refined version. He brought drawings to a local machine shop to have it produced.
I asked Jon why, after having a workable if ugly self-built prototype, he bothered going to the trouble of having a machine shop create a refined one. "Because the original, crude prototype showed that it worked," he said, as if having one professionally fabricated was the next logical step. "My initial idea was that this would be a tool for myself," and it might as well be a proper one.
With his new, unnamed tool, Jon continued harvesting firewood, now at an accelerated rate. But more important than the greater efficiency was the simple fact that the work was now easier on the body. He didn't have to bend down to pick up logs, nor risk a vicious injury from the pulp hook.
Jon with current-day production version
Multiplying the Multi-Tool
While using the tool, "it occurred to me that if this is something that is very helpful to me," Jon says, "I'm sure it would be quite helpful to somebody else." As far as Jon knew, there was nothing like his tool on the market; you'd have to buy three separate tools, and carry them all into the woods, to achieve the same functionality.
Due to his product development experience, he instinctively checked if anyone else had developed a similar idea. "Because I was very familiar with going through the patenting process, I [figured I'd] take a look and see what prior rights might be available out there."
"I did quite a bit of research on it," Jon says, and after an exhaustive patent search process "couldn't find anything that was exactly what this is." His design was unique. It was useful. He reasoned that if they were in mass production they'd sell, and he applied for a patent on it. But as he was still employed at the time, he'd decided "I certainly wasn't going to manufacture it myself."
Instead Jon looked for a manufacturing partner. "[One approach is to] find somebody who is actually marketing towards the same customer base as your tool would fit," he says. Since he was using the tool to bring logs to a wood splitter, he figured others would too, so a company that made wood splitters would be a good candidate.
One such company Jon identified was Swisher Inc., a Missouri-based manufacturer of log splitters, zero-turn mowers, string trimmers and other nature-taming machines. They manufactured their products in America, an important factor for Jon. And by examining their product line-up, he saw that they possessed "good mechanical engineering expertise. They know how to deal with metal. They have good welding. They have laser cutting. They have, very importantly, powder coating capabilities."
Swisher's manufacturing facility
He reached out to them: Would they be willing to sign an NDA, to look at a new invention potentially relevant to their customers?
Their answer was yes. And "one day in late 2014," says Chris Connell, Swisher's Director of Operations, "I received a small package in the mail from Jon Roberts, with a product idea for a forestry logging tool." Connell evaluated Jon's design and found it "a very innovative tool, [it] turned three separate logging tools into one multifaceted tool."
All three functions
Swisher primarily manufactures power machinery, things with engines attached to them. I asked Chris why they decided to manufacture Jon's non-powered tool. "[We saw it as] an opportunity to expand our manufacturing away from our traditional product lines," Chris explains, "with a product that complimented market segments we were already serving. And it fit well within our manufacturing processes." Jon had identified his target well.
A Rocky Launch
By 2015 Swisher had agreed to produce the tool, but this was a partnership, not a licensing arrangement. In order to retain rights to the tool and see any potential profits, Jon and Lynne would have to have some skin in the game, meaning they'd fund the production costs.
2015 version of the LogOX, made from flat bar stock
The Robertses soon found themselves in a classic inventor's pickle, where you have a good product, a brilliant one even, that isn't selling at scale. A lot of money goes into getting a tool off of the ground, and there wasn't enough money coming in to recoup their investment.
The problem wasn't the design of the tool; the problem was that no one had heard of it. To spread the word Jon began driving around New England with the first version of the tool. "I mostly approached small shops that were servicing chainsaws. We felt that anyone who owns a chainsaw, log splitter or portable sawmill could benefit from using a LogOX (as the tool would come to be named). The reception by the shop owners, most of who had been in the business for many years, was extraordinarily encouraging." But it wasn't enough, and on top of that "it turned out that there were a number of unexpected manufacturing issues that threatened to drive the cost to a point that would make it impossible to market."
Jon worked with Swisher to refine the design and improve its manufacturability, switching from a flat handle that required bolting the attachments on, to using tubular stock and quick-change clevis pins. This brought the cost down while improving the user experience of the tool.
Clevis pins, faster to remove than bolts, and no wrench required
The Robertses had a lot riding on this redesign; by the end of 2015 Jon still had no income and they'd taken a loss on the tool, and he hoped the changes would reverse that.
In the meantime Jon continued using the tool himself, steadily putting up firewood for the next winter. I asked Jon and Lynne how much firewood they burn each year. "Between four and six cords," they said. [Editor's Note: A cord of wood is a stack that's four feet deep, four feet high and eight feet wide.] They'd been burning this amount for as long as they could remember. Firewood kept them warm as a newlywed couple, and later as a family, when their children were born. In fact, son Austin told me, some of his favorite memories from childhood were of being in the living room around their wood stove, warm despite the biting New England chill.
From ROTC to PsyOps
Staying warm was no longer a problem for Austin, aged 25, as he was doing foot patrols in Afghanistan's Kunduz province, where the temperature could top 130 degrees Fahrenheit. As a Fire Support Officer for the 10th Mountain Division's 1-87th Infantry*, Austin and his unit were clearing the Gortepa Valley of Taliban strongholds. He was a long way from Vermont, and instead of carrying the firewood he'd helped harvest as a boy, he was loaded up with "anywhere from 70 to 90 pounds of gear, once you factor in your body armor, assault pack, weapons, ammo, et cetera."
*[Editor's Note: "1-87th Infantry" means First Battalion, 87th Infantry. If you're curious to read more about what Austin's battalion experienced, the New York Times covered the 1-87th's yearlong action in Afghanistan in an article series called "A Year at War."]
This was in 2010-2011, and one of the incidents that had motivated Austin to join the Army in the first place had transpired roughly ten years earlier. On September 11th, 2001, a 16-year-old Austin was "sitting in my high school English class when the first plane hit the World Trade Center," he recounts. "My teacher, a Long Island native, turned on a small radio and we listened to the events unfold intently. By the middle of Geometry class, the second plane had hit the Towers, and it dawned on me and my classmates that we were now a nation at war. I felt determined to do my bit in responding to these attacks.
"My grandfather had fought in the army when Pearl Harbor happened, my great grandfather had fought in the Army during World War I, all the way back to the Civil War and the Revolution, my family's been in the Army during times of conflict and war. So that's what I decided to do. I saw it as my patriotic duty."
While he planned on the military being his career, he decided to go to college first, and earned a degree in Government and Military Science from Georgetown University. I asked him why the university pit-stop, when he could have signed up at 18?
"I was a scholarship ROTC cadet," he explains. "Studying modern military science was part of that. The 'Government' part of the degree was essentially political science, the idea being that I wanted a well-rounded liberal arts education, and to learn how government and political systems work.
"Especially in a counterinsurgency type of war like we found ourselves in [after 9/11], a lot of emphasis is placed on good governance, and being able to help our allies achieve good governance. If you look at what's being going on in Afghanistan, a big part of the push there is helping them with that. So I wanted to have a good background, a good understanding of that to set myself up for having a career in the army."
Austin Roberts in Afghanistan, 2010
After a year in Kunduz, "We were able to clean up that area and hand it back to the Afghans," Austin says. Over the next few years his career progressed with a series of promotions and training; he worked his way up to Battallion Targeting Officer, then Operations Planner, then Psychological Operations Officer, with postings in Qatar and Germany along the way. By 2015 Austin, who'd entered the Army as a 2nd Lieutenant and was now a Captain, was working at the State Department in Washington, D.C. as Liaison Officer.
But while he was happy with the work, something else was tugging at him. "I'd planned on serving a full career in the military, and I liked what I was doing," Austin says. "But I'd met my then-girlfriend, now wife, my senior year at Georgetown University. After I entered the Army we basically had an eight-year long distance relationship while I was deploying all over the place." His wife was now finishing up med school and soon to be assigned a three-year residency in a random part of the country. If that happened to be in D.C. and Austin retained his post there, no problem; but what were the odds of that?
In December of 2015, Austin's wife was matched to a hospital outside of Philadelphia. Austin realized no military posting would bring him to that region, so as 2016 unfolded he made a tough decision. "My service obligation would be finished at the end of 2016," he says. "I decided to move on and finally be co-located with my wife." He wasn't sure what he'd do for work, but he figured his military and planning experience could land him a job in consulting.
In June of 2016, Austin learned that Jon had been laid off. And like Lynne, "wasn't terribly worried about it," he says. "Jon is one of the most hardworking and competent people I've ever met in my life--and I've met some very high performance people in the military and working with senior level diplomats. I thought [his being laid off] was a weird anomaly, and I had no doubt that he was either going to find another job, or make one."
Taking a Bold Gamble
While Jon was trying to figure out how to re-enter the industrial world, Lynne, who was descended from a long line of lumberjacks in Maine, had an idea for swinging the family back towards forestry. "Jon, this is a fantastic tool," Lynne told him, after he'd experienced yet another job rejection. "We just need to get it out there. We need to do the marketing part of it."
"I give Lynne a lot of credit," Jon says. "She had a strong, strong vision, a feeling that the LogOX was something that we should focus on."
He had some reservations. "It was an unnerving and difficult decision to abandon the traditional job hunt and place all my efforts into developing a market for a new and unknown logging tool," Jon says. "Naturally, funneling money away from funds set aside for retirement to bootstrap a new enterprise was also a truly scary idea."
Coincidentally, that same summer that Jon was laid off, a package arrived at their house from Swisher. It was the latest iteration of Jon's redesign, still in prototype battleship grey. The timing couldn't have been more fortunate; if Lynne saw Jon's downsizing as a Godsend, this was clearly the second part of the divine delivery.
At Lynne's urging, that August they brought the tool to the Green Mountain Fair, an annual country fair in nearby Manchester. They set up a pop-up tent they'd purchased and rolled out a few log rounds to demonstrate how the tool worked. Many of the folks who saw and tried the tool responded with enthusiasm.
Two weeks later, the first production run of the redesign was ready, in the finished orange color:
Jon and Lynne brought them to more events. "After going to a number of fairs and trade shows and seeing how people were reacting to our new multitool, our confidence grew," say Jon.
However, he adds, "We were still operating in the red." The redesign was undoubtedly an improvement over the previous iteration, but as 2016 came to a close the Roberts had sunk more money into the tool than they'd received in profits. They simply weren't selling enough of them.
Smart Marketing
As 2017 began, Austin's military service was completed. He and his wife had another six months to go before they'd move to Pennsylvania for her residency, and Austin began looking for work. "I had interviewed with a couple of different consulting firms, was talking with others, and waiting for which opportunity I wanted," he says.
While still in the service, during his off-hours Austin had helped his folks set up their website. Now, with a half-year before he could fully commit to a new job, he had more free time, and began helping them out with the marketing.
I ask Austin if he had any background in commercial marketing; the answer was no. But interestingly enough, his military training gave him a leg up with this seemingly unrelated field. "As a Psychological Operations Officer," he explains, "part of what that job entails is strategic communications on policy issues. So I had a decent understanding of how the media works, how to create compelling narratives, how to reach out to various target audiences and be able to get a message across to them.
"Like with everything else, I threw myself into it," he continues. Just as he'd attended college before joining the Army, in order to better arm himself with knowledge, Austin studied the problem first. He read articles and books about marketing, studied online social media marketing techniques, followed startup companies to see what they were doing and how. "Before I knew it I was spending 90% of my time working on the LogOX," he says, "and 10% of the time hunting for another job."
As with the military, book learning will only get you so far, so Austin spent plenty of time in the field as well. "We [set up a booth at] various trade shows and homesteading shows, which was very useful. [You need to] figure out who your audience is, your ideal customer, where do they go, what do they read, what are they interested in, and try to interject yourself in that conversation.
"As a marketer, being at the shows is really invaluable. Meeting and talking to people helps with word of mouth. And getting comfortable with the details of demonstrating your product, so that when you're sitting behind a computer and writing sales copy, you're able to take the feedback that people gave you, realize what the frequently asked questions are, and tailor your message to something they would find interesting, that answers the questions that they have."
Austin's plan: "To figure out the most cost-effective way for us to get our product out there," he says. "We knew we had a great product and we knew it would sell, because we use it ourselves and realize how useful it is. We just had to get it out there to enough people so that they would also see the value of it."
Led by Lynne, at that point the Robertses decided to go whole hog. They formed an S Corp and trademarked the name American Tools for Woodsmen, which their company would now be called. Jon would be the product developer and Lynne, "who was driving much of the company vision, would have main control and be President," Jon says. They named the tool the LogOX, in a nod to the days when "oxen were used as powerful animals in the harvesting of wood," Jon says. The company's mascot is a blue ox, in reference to Paul Bunyan's famous bovine sidekick, Babe.
Austin's role would be General Manager, and he'd tackle the marketing. "One of the primary reasons for bringing Austin on board and founding the company as it is today," says Jon, "was to help us with our sales and marketing outreach, both to potential customers and retailers, demonstrating how the LogOX can truly benefit them."
After studying the problem, Austin figured out how to execute his low-cost way to get both exposure and feedback on the LogOX. He identified popular YouTube channels run by homesteaders and outdoors-people and sent them a LogOX, strings-free. If they found the tool as useful as the Robertses did, Austin reasoned, they'd probably make a video about it; if they didn't like the tool, he could ask them what the company could do to improve its design. In the short term he'd be losing money by sending out free tools, but if the tool was as good as they thought it was, it would pay off in the long run.
"Marketing is all about creating demand," Jon tells me, "sales is about fulfilling it." As it turns out, Austin wound up doing such a good job with the former that it was the latter that came up short.
"We had spent the entire fall sowing those seeds, and after hitting the road and going to a bunch of different shows, review videos started popping up all over the place on YouTube," Austin says. "We had been growing our social media, and the day before Black Friday we actually sold out. We had to take it off of Amazon for about ten days until we got more products on board."
The Roberts at a UPS center in 2017, shipping out LogOX's for the holiday rush
"Financially," Jon says, "2017 ended in the black--barely--which we considered a huge success."
By 2018, momentum had formed. Much of the groundwork Austin had laid was producing exponential results; YouTube review videos--from people Austin hadn't even sent a tool to, but who had seen other videos of it and subsequently ordered one--began popping up like dandelions. Indeed, that's how I first learned of the tool.
Made in the USA
Last year I permanently abandoned my hometown of New York City to live on a farm down South. I quickly learned it's a very physical existence, and began absorbing a lot of material on YouTube to figure out the best ways to prosecute various farm tasks. The harvesting of firewood is a particularly labor-intensive one, and seemingly every channel I watched for labor-saving firewood harvesting tips featured a LogOX.
One video by Swedish Homestead struck me in particular. Simeon, the German host of the channel, was describing the LogOX and pointed out that "This is an American company and it's made in the U.S., which I really like. Right away when I opened the bag and I felt the stuff, I felt that it's really strong, powerful stuff."
Simeon demonstrating a LogOX on Swedish Homestead
That statement struck me because I'm used to hearing Americans rave about German tools, not the other way 'round. For roughly the first half of the 20th Century, American-made tools and products were tough to beat; but these days, even heritage American brands--names that your father or grandfather grew up with and trusted--often manufacture overseas, with poor or inconsistent quality. And nothing is worse, at least to me, than buying an American-branded tool and discovering it's a cheaply-made piece of crap.
But here was Simeon, one of the online leaders of the homesteader movement, a native of a country that makes great tools, complimenting the build quality of an American product.
The fact that the tool is American-made, and to a high standard, is important to the Robertses; indeed it's part of the company's ethos. "One of the cool things about starting and running your own company is that you can set your standards," Austin says. "Our company's called American Tools for Woodsmen, and our standards, for reasons of both quality control and to employ our fellow Americans, is to make a great product here in the 'States."
I ask the Robertses the question a lot of successful entrepreneurs have to grapple with: What if a big box brand approached them, offering to increase their distribution by a factor of 10, if they would lower the cost? Meaning that they would have to whittle down the Bill of Materials and/or manufacture overseas?
"We've already had people come to us and [offer that kind of deal]," Jon says. "But if you look at our reviews, you'll see that firstly, our customers appreciate that it's American made. Secondly, that it's beefy. There's a lot of workmanship in there. If you want to bring down the price, you're going to have to cheapen a lot of the way you're doing things."
"Which is a non-starter for us," Austin adds, "for two reasons. One is that we'd be lowering the quality of the product itself, and the other is [that a lower pricepoint would require] making it somewhere outside of the United States. So that's not going to happen."
And in fact, as of recently the LogOX actually is available for purchase at big boxes, albeit through their eCommerce sites. "In 2018 we more than tripled our sales from 2017," Jon says. "We started to create some real volume, and as of about six months ago, with our manufacturing partner we are now on the e-platforms for Lowe's, Home Depot, Tractor Supply. We're not inside the stores; it's a step-by-step process, where they said "Let's walk before we run. We like the concept of the tool, so let's bring it onto our eCommerce platform, see how it's working there, and then the next step is to put it onto the floor." It's worth noting here that the LogOXen carried by the big boxes is not a watered-down version, but the same tool you'd get from any LogOX distributor.
Quantifying Success
About four years ago I injured my back trying to move a 24,000 BTU air conditioner, and managed to cause permanent damage. That incident is one of my greatest regrets in life, and I urge all of you able-bodied to never try lifting something you cannot because you are afraid of looking weak in front of onlookers; the permanent, lifelong pain is not worth it. Here on the farm, if I am not careful in how I hoist 60-pound bags of concrete or even 50-pound bags of animal feed, I can easily reaggravate the injury, and spend the next few days lying to my wife when she asks if everything is okay. So when I saw the kind of lifting that is required to harvest firewood, which is a task I need to perform here, my heart sank.
The LogOX is one of those tools that makes an immediate difference. As soon as I tried it, I found that due to the carefully-considered geometry of the tool, it requires almost no effort to pick up a log round. The weight of the load is in line with the way that your arm naturally hangs from your shoulder. Loading rounds onto the bed of a pickup or the back of our farm Rover (I don't own a splitter) is rendered easy, compared to the purely manual alternative. It's one of those tools that is such a clear improvement over what came before, that you look forward to performing the task it was designed to ease.
In this case I bucked up a log that had rolled downhill. Using the LogOX to carry the rounds back up was easy
[Editor's note: Prior to writing this article, I requested a LogOX from the Robertses to test out. They sent one, free of charge. After evaluating the tool, I paid them for it in full, out of my own pocket (not Core77 money). I decided to write about this tool because I use it and value it highly.]
All--not some, all--of the YouTube reviews I watched on the LogOX mentioned how much easier it is on the back. But my experience, and the experience of the other users, is all anecdotal. The Robertses wanted to get some hard science on the ergonomic benefits, and they're now working with an engineering school to quantify it.
"It's one thing to have a lot of positive reviews from our customers saying that this is an ergonomic tool," Austin says. "It's another thing to gather scientific, empirical data that shows exactly what it does for you. We've partnered with Fairfield University's engineering department on a year-long process, which we're halfway through at the moment. We want to be able to show the ergonomic advantage we have in a way that's measurable and observable. We'll then put that together in an overall report that we have as a sourced university study."
The Future of the Company
American Tools for Woodsmen is not going to be a single-tool company; Jon has already invented, and they're already selling, another gamechanging item with clear ergonomic improvements called the WoodOX Sling. (We briefly covered this object here, and will discuss it along with Jon's innovation process in a future article.) Furthermore, at press time Jon had secured a patent for a third object beyond that, details of which are still under wraps.
And the LogOX itself may evolve. For one thing, the Fairfield University collaboration is meant to highlight ways to optimize and improve the tool. Secondly, the existing extension handle is designed in such a way that a purpose-built hook can be attached to it, turning the extension into a standalone pickaroon (a tool for moving log rounds at a distance).
That attachment point "opens up a whole wide world of different types of attachments and things that we could put onto that," says Austin, mentioning that they're doing R&D in that area now.
In the meantime, Jon will keep inventing, Austin will keep marketing, and Lynne will continue doing outreach. As one example of her patience yielding a payoff: Back in 2016, when they'd first hit the trade show circuit, Jon & Lynne had met an executive who worked for a tree service company. She liked the LogOX, and she and Lynne had kept in touch. That woman turned out to be Kathleen Gorman, who started her own company, Diverse Supply Solutions, in 2018. Gorman's company is now, in 2019, a LogOX distributor.
The larger example of Lynne's vision paying off is, of course, that she suggested they commit to Jon's invention in the first place. She's a lot busier now than before LogOX, but doesn't seem to mind: "While we're working practically 24/7--customers always marvel that we respond to them very quickly, even at night and on weekends--every morning I look forward to walking upstairs to my office and fielding calls and emails from our customers," Lynne says. "A common theme, and frankly the most rewarding part of those conversations, is hearing about the different ways the LogOX has made a big improvement in their lives. We'll hear from somebody who has just had back surgery, or is 86 years old, and finds the LogOX helpful."
"Transitioning out of the active duty military can be a difficult process for any Veteran," says Austin, reflecting on his decision to go all-in and co-found the company. "Going from a regimented lifestyle with clear benchmarks for career success and relative financial security to the roller coaster ride that is entrepreneurship, is particularly challenging, especially when also supporting a family. However, I've found the forestry industry and homesteading community to be full of great, hardworking people, and being able to provide them with a useful tool like the LogOX has been tremendously fulfilling, making the entire process worthwhile."
Jon, Lynne and Austin Roberts
"Starting a business is every bit as difficult as you hear it is," Jon says, "but the independence is worth every ounce of energy, especially when the business starts to grow and become increasingly successful." And, of course, there's little chance Jon will ever worry about being downsized again.
Jon with an early prototype alongside the current-day production version
How Neuroaesthetics Will Shape the Future of Design
Unexpectedly, one of the few installations at Milan Design Week that resonated past the thick, blurry Instagram lens wasn't created just by designers. Google's A Space for Being (in collaboration with Muuto, Reddymade Architecture and the Arts + Minds Lab at Johns Hopkins University) provoked deep thoughts about the future role of technology in intimate spaces like the home by bringing visitors into a world where their only requirement was to 'be'—no cell phones and no talking allowed.
Before entering the space, a colorful screen-less band was placed on the wrist to measure each individual's reactions, like heart rate and skin temperature. Upon entering, winding hallways led you through three separate rooms, each designed with different furniture (all by collaborator Muuto), textures, books, color schemes and even scents. At the end of the experience, the bands were collected and the data was interpreted by Google, revealing which of the three spaces the algorithm felt you were most 'at ease' in. For Google, this installation was less about designing the next best wearable and more about demonstrating the potential for this technology to influence the design process, whether it be conducting user research before designing a new appliance, or even redecorating a home based on what makes the owner feel most comfortable.
After experiencing A Space for Being ourselves, we sat down with Ivy Ross, VP of Hardware Design at Google, to learn more about the collaboration and to hear her thoughts on technology's role in the future:
When I initially read this installation would be about neuroaesthetics, I thought it would be depicting this scary sci-fi world, but I was shocked to see that it's quite the opposite.
I'm so glad that we surprised and delighted you! Last year when we showed up people said, "oh the tech giant showed up so unexpectedly human". Well yeah, because that's what we are. Us being here is about being a thought leader. We really want to share with everyone the way we think and how thoughtful we are when we design product.
So how did the idea for A Space for Being come about?
It all started last year when Muuto saw our installation here in Milan and said, "Oh my god, we love your aesthetic", and we said, "We love your aesthetic!" We had pictures of their dots up on our wall at the time. They brought up the idea of doing something together for this year, and I just didn't want to put our home products in their living room settings. That would be really boring.
Photo: Maremosso
Two years prior, I had been contacted by Susan [Magsamen] in the Arts + Mind Lab at Johns Hopkins. She told me that she runs the Arts + Mind Lab, and that they were studying something called neuroaesthetics. I didn't know what neuroaesthetics meant, so she explained to me that it's the study of the effect that aesthetics have on the brain and the body. I know the effects it has because I've been a designer and an artist my whole life, and we know that intuitively. But wow, if neuroscience can prove this, than that could be such a great support system for designers.
I also met Suchi Reddy of Reddymade Architecture a few years ago. She is designing a room in a hospital for kids who are coming out of comas to help knit back their brains each sense at a time. It's a beautiful project, so I put them in touch.
I called both of them and said, "Ladies, I have an idea. Can we actually put people through living situations?" I wanted it to be like real life, not some art project. We could make bands with sensors, and Johns Hopkins could help us make an algorithm. We decided to pick at the feeling of 'ease' because it's the opposite of stress, and right now I think there are a lot of stressed people in the world. We could've picked anything, right? I mean excitement is good, being relaxed is good... so we picked this phrase "at ease". We did a lot of research to find a phrase that everyone understands.
"Preference and taste are so individual. I want the world to go in a way where we're amplifying our own individuality, we're not trying to be like each other. We're celebrating who we are."
The idea was to show that we are in control of our environments. Everything affects us, and we have agency over that. I think we've gotten a bit flat lined as a society. Aesthetics isn't just making something look pretty, it's awakening all the senses. And we can do that through an appreciation of all of these different elements—sound, light, color, texture.
On that note, everything within the space and the user experience is so thoroughly executed, down to the data presented as a piece of art. This is, of course, something that appeals to designers because it's a beautiful presentation, but it also makes data more readable for people who aren't designers. Is this something you considered during the design process?
This is the greatest gift for all this hard work, that you get it. For designers that are here experiencing this, we want to support them and tell them that what they do matters. For people that aren't designers, we want to tell them that design matters. Everything you encounter matters. What you choose to surround yourself with matters.
Preference and taste are so individual. I want the world to go in a way where we're amplifying our own individuality—we're not trying to be like each other, and we're celebrating who we are. But in order to have any insight into who we are, we need to understand that who we've been and everything we'll become is a byproduct of what we have experienced.
The data presented at the end looked like a piece of art—the bigger, warm splotches represent spikes in excitement, while the thinner, cool splotches represent moments of zen. Photo: Maremosso
I love that people are telling me how surprised they are that the data is coming out as this beautiful art piece. The data is a series of numbers that feed into this system, but the truth is that the output in the infographics could look like anything. My team worked hard on devising how to use the spread of the ink and bursts of color to indicate one thing versus another.
This installation is obviously one scenario in which this type of data collection can be applied, but do you see other ways in which it could be useful?
Even in the Google School for Learning, we've started to think about what the right environments are for learning. There are certain neuroaesthetic things that actually encourage retention, memory and learning. So I think its just a matter of being aware. The research around this has been going on for 20 years, but only in the last three years has it come into the applied area—out of the science realm and into real world applications. This is pretty much the first exhibit that talks about it.
There are definitely implications in terms of applying this to homes. I don't want to see a world where we're all striving for the same chair or the same table. What's right for one person is not right for another. In different situations, I think this could amplify that. You think we're riding the elephant, we're controlling the elephant but the elephant is really controlling us, and the elephant is the subconscious. Are we saying we love a specific room because that is the room we believe is the prettiest or the one that we should like versus how our body actually feels in it. So in homes we should not get obsessed with it but just use it for a little bit of self knowledge.
Do you think being comfortable is more important than being surrounded by beautiful things?
Not necessarily. Some people equate being calm with being bored. And you know, being bored is a mental construct, but being calm is a physiology thing. What we are finding is healthy for our body is being in that calm state, where we're not excited or stressed all the time. But we live in a world where we're optimizing everything all the time.
Photo: Maremosso
I'm interested in this idea of finding those calm places beyond the spa where we can just be chilled out, so I particularly picked the home environment because it's an environment that you can control. So for me, I designed this modern tree house for myself. Anything could be going on at work, but when I come home to the trees, sit on my couch and look up at that forest—I can just feel it.
People say to me, "oh you have so much responsibility at work but you're so calm". I think it's because I've learned to know what works for me. There's all this pressure for us to meditate. It's about finding that calm at times, which you can do even just by listening to the right music and just being. We've asked you to not have your phones in [A Space for Being] because it should just be about being. For some people it's really hard to spend five minutes—it seems to be a real treat that we have to give ourselves permission to do. But it's really important that we do it. So A Space for Being is just a little exercise to remind you that you are in control of finding a peaceful environment.
When I first saw the bands, I was surprised to see that they are screen-less and don't send out notifications. They weren't bossing us around like we're used to. Is silent but helpful the next wave of wearable tech?
The band, which is currently not a commercial product, was done for this exhibition, but it does represent our philosophy that tech is able to amplify our humanity and that it can be here to help us. It's what we do with it that matters. This is a prime example of an indication that tech should give you information about yourself without being scary—just helpful.
Photo: Maremosso
It's just like Google Maps—how did we live without it? Before that you had to carry a thick Thomas Guide in the passenger seat. I don't know how we didn't get into more accidents because how did you even look up A9 on a grid while driving? Anyway, even though the band is just for this exhibition, we were very thoughtful with how and why we were doing it.
Oftentimes, technology acts as a way to disconnect from your emotional intelligence. What you're envisioning is instead a way of using tech to better understand yourself and what you need...
Absolutely. We have dug these pathways that thinking and feeling are two separate things. We think we're being smarter by operating from our neck up and always being in our heads, but we forget that the body is an incredible barometer.
Did you see the movie "Her"? It was such an impactful movie to me. It came out right before I took this job at Google. I remember thinking that it was an interesting example of where technology actually helped someone learn more about themselves than any shrink or anyone else seemed to be able to. Now I'm not suggesting that we walk around with an operating system like Samantha, but technology that is additive to your life instead of taking away humanity is the type of technology that my team and I are interested in.