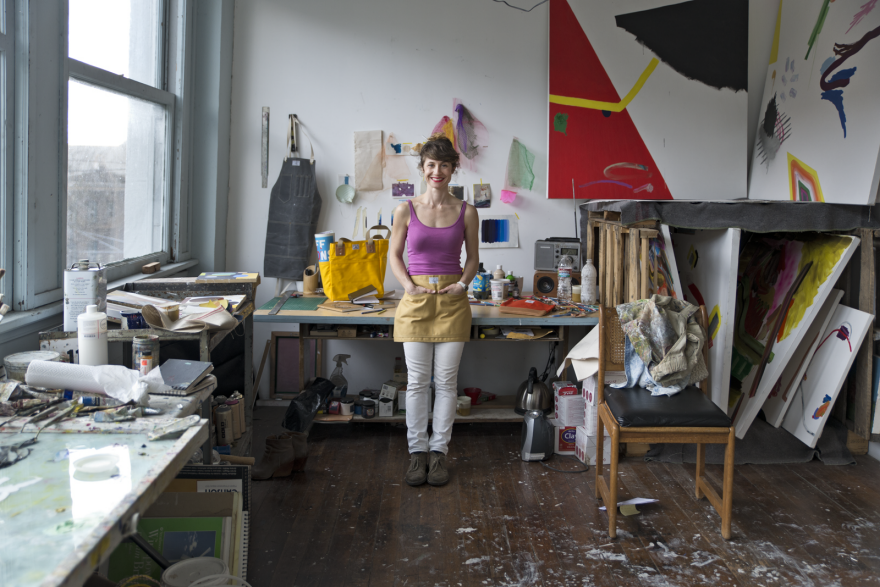
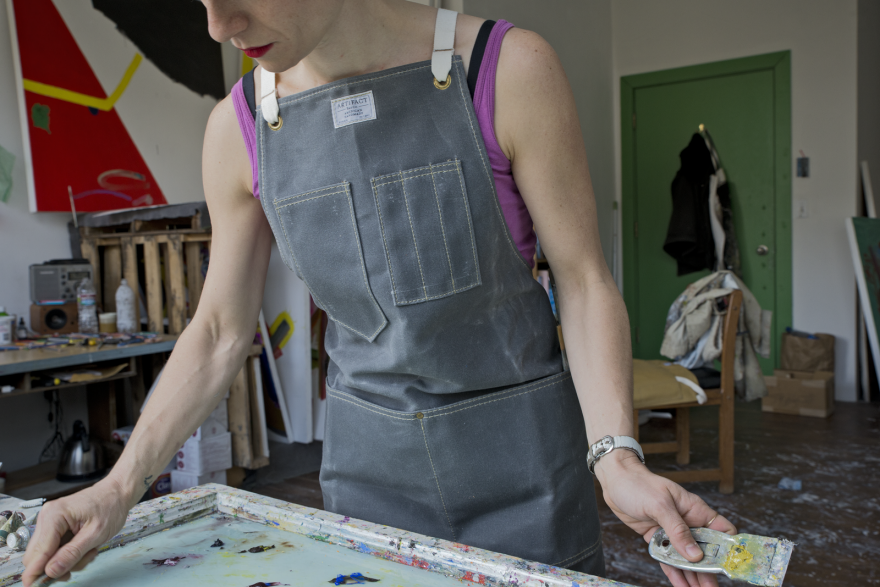
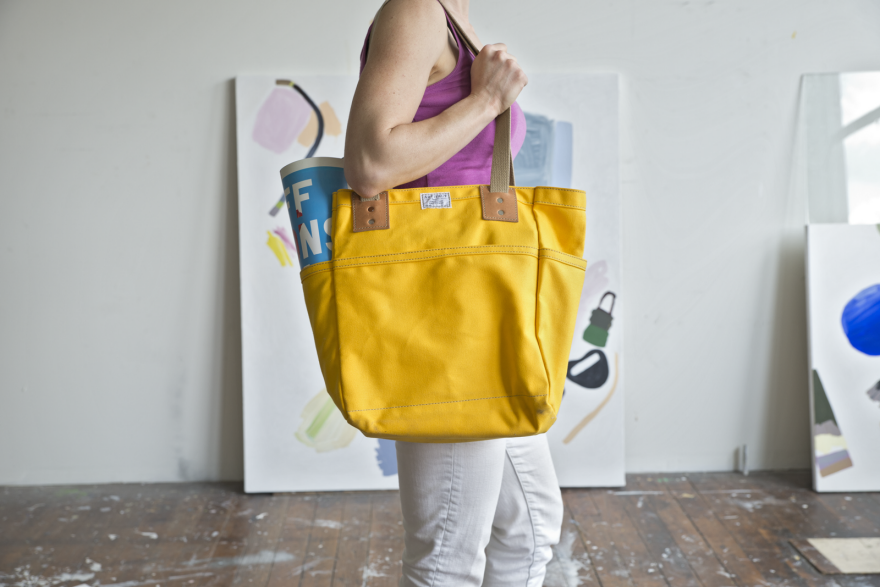
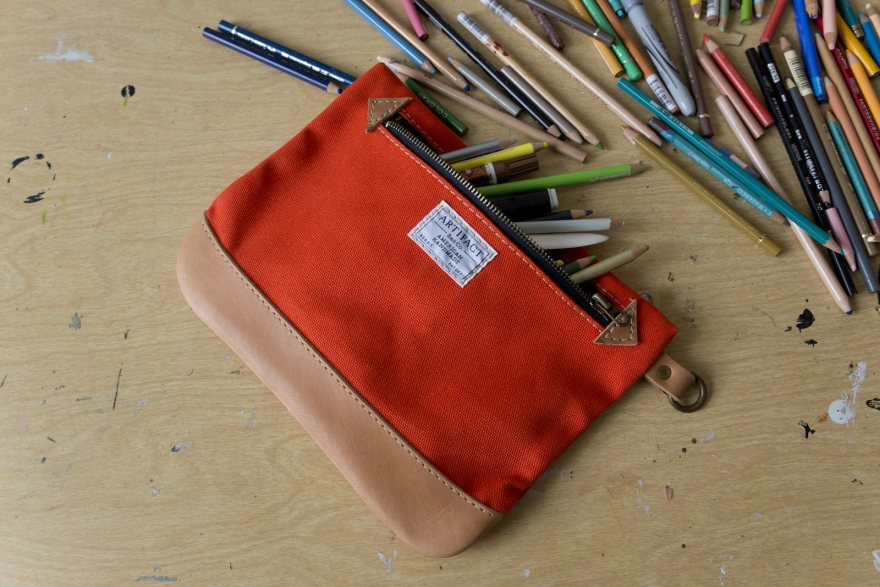
One of my pet peeves is that I can't find durable footwear. Every year my sneakers seem to wear out faster than the year before.
But that is a lament of the privileged. For children in developing nations who are lucky enough to get shoes, they do not last long no matter what their construction, because children outgrow them. Thus Kenton Lee, who formerly did missionary work in Nairobi and witnessed this firsthand, has invented a shoe that can be adjusted to fit growing feet.
Lee collaborated with ex-Adidas and ex-Nike veteran Gary Pitman to create The Shoe That Grows, a durable leather and rubber sandal with snaps and buckles for size adjustment. They've gotten the price down to just $10 a pair, and can stuff 50 pairs into a duffel bag, which they then ship off to developing countries around the world. And they're designed to last for five years.
As you can see, the clever design can expand at the heel, at the toe, and laterally.
The need for these shoes far exceeds simple human comfort; without them, children are susceptible to groundborne parasites and simple cuts that can get infected—which turns into a major problem in underdeveloped areas.
Over 2 billion people suffer from soil-transmitted diseases and parasites. They live in areas that do not have adequate sanitation. They struggle with proper hygiene. They do not have the right clothing, resources, or health coverage. And being sick = struggling. Kids miss school, can't help their families, suffer with pain. Many of these diseases and parasites get into the body because people don't have shoes.
Next Order of The Shoe from Because International on Vimeo.
Happily, the team's currently-running crowdfunding campaign successfully hit their $50,000 target (though you can still donate by hitting that link if you'd like to help).
Let's say you're a designer trying to create something with moving parts: A set of double doors that open in an unusual way, a console that deploys a hidden flatscreen monitor, or a space-saving cabinet with panels that slide sideways rather than swing out. Where do you start?
There are companies that make hardware to achieve these things, but there's no guarantee that hardware is sized to fit your application. If you can understand how the mechanisms work, however, you can create something to custom fit your design.
That's where this retired mechanical engineer comes in: Nguyen Duc Thang has made it his mission to illustrate mechanisms so people can understand them. Using Autodesk Inventor, he creates succinct 3D animations of various mechanical mechanisms, and staggeringly, he's created 1,700 videos of them to date.
As an example, check out this mechanism for double doors that open within a limited space:
An overhead-concealed monitor mechanism:
Three different ways to get cabinet doors or window covers to slide sideways in concert:
Here's another take on the concept, where the doors move in the same direction:
Those interested in how things are made will find a lot of production-method-based animations on Nguyen's page, too. Did you ever wonder how they turn things with undercuts, like doorknobs? Here's how they get the plug out:
Nguyen's exhaustive list is also filled with pure mechanical phenomena, like this rotating contraption that keeps the panels atop it aligned:
Or a way to convert reciprocating motion into rotary motion:
All in all, Nguyen's YouTube channel is so dense with videos that you're bound to find something interesting. And because the collection is so thick, he's created a freely-downloadable index of it all here, with descriptions and photos, so you can search more efficiently.
Via Kottke
With the IKEA temporary show that included a concept kitchen, Milan was abuzz discussing the future of flat pack shipping and embedded technology. IKEA's charging-hub furniture became available to buy for the first time and their own Björn Block spoke at frog Milan about the future of their stores and distribution. All of this talk had us asking ourselves - does it even matter how we ship? In the 'Future' won't we just be sending files to local distributors? Will flat pack even matter?
One of the few places during Milan 2015 that open source and distributed manufacturing did enter the conversation was at the historic Palazzo Clerici. The Atilier as one of the most classic italian exhibition spaces of the week was home to some of the most progressive ideas and products of design week. Here are four of our favorites that touch on the future of tech and design.
Open Making Platform by Opendesk
The platform and database Opendesk shared their vision for a future of making and distributing furniture and objects through open-source sharing of designs. Their 'Open-Making Model' allows a network of independent designers to upload designs on the site that is accessible by anyone. People interested in owning one of the designs can search through the database of CNC Routers and digital fabrication locations and find and select a closeby place to cut their new piece. This method requires little (if any) shipping and distribution costs and allowing designers on their platform a global customer base.
For many of us, a transparent understanding of how everyday products are made has been lost. Now, as power shifts from the old economies, we are forced to consider new possibilities. Through emerging, connected technologies we can begin to imagine a more socially, environmentally and economically conscious model - a democratised means of production fit for the 21st century…and in the process, we have the chance to locally reconnect with the act of making.
Hacking Households by Leonardo Amico, Thibault Brevet, Coralie Gourguechon, Jure Martinec, Nataša Muševic with Mentors Tilen Sepic and Jesse Howard
Under the guidance of none other than Jesse Howard and Tilen Sepic, the Hacking Households team developed a series of objects from a set of modular components that act in the same way blocks of code do in open source software. The team developed a series of adaptable objects that can reconfigure, be forked or hacked to the user's preference.
Amsterdam-based Jesse Howard has become known for his open sourced designs, giving power back to consumers to hack and build their own domestic objects. In Database Lamps the design begins with standard manufactured dimensions for table top lamps, a special user interface allows consumers to generate their own components for 3d printing their own variations of the classic balanced-arm lamp.
Paper User Interfaces and Paper Electronic Modules by Leonardo Amico and Coralie Gourguechon
Last but not least was a playful project from Leonardo Amico and Coralie Gourguechon. Paper User Interfaces 'PUI' and Paper Electronic Modules 'PEM' explore electronic circuitry built with paper.
Using conductive ink, personal ink-jet printers can be transformed into circuit printers, suggest a future in which electronic appliances can be cheaply and easily printed at home. PUI combines this technology with an analogue interface and digital touch-based gestures, showing electronic functions through graphics and 3D shapes.
More work from Atelier Clerici during Milan Design Week can be seen on their website.
Chauffeurs can get uppity, and it's no wonder: They're entrusted with driving your six-figure luxury vehicle, and just as you sit in the back with an empty seat next to you, so too is there an empty seat next to the chauffeur up front. This may give them the illusion of parity, or that they'll one day have a companion to sit next to them and keep them company on those long drives to the airport, and that sends the wrong message.
But not with Volvo's XC90 Excellence Lounge Console concept, designed for the discriminating executive.
The designers have ripped the front passenger seat out altogether and replaced it with a multifunctional object. At first glance, it's a shoe cabinet.
This conveniently deprives the chauffeur of a place to keep his personal effects, with the added bonus of allowing the passenger to take their shoes off and place their aromatic feet much closer to where the chauffeur can smell them.
A pop-up tray contains a 17-inch LCD monitor and doubles as a jewelry tray, with a large mirror that flips out of the rear.
There is also a lockable compartment where you can store an array of expensive watches that cost more than the chauffeur's annual salary; it cannot hurt, we think, to mention this aloud as you bring each watch out to model it.
Admittedly the design is not perfect, as the executive may wish to sit on the left-hand side and still stretch out. Ideally there would be some way for a left-riding passenger to recline, extending their shoeless feet to either side of the chauffeur's head. But until they work that out, we'll have to settle for this:
Many of us would love to see one of our product designs for sale at a large retail chain. But when Aaron and Claire Van Holland saw their mirror selling at Urban Outfitters, they were less than thrilled. The reason: They never sold their design to Urban Outfitters!
The Van Hollands—the design duo behind the small L.A.-based brand M.F.E.O.—were "beyond disappointed to find a cheap knockoff of our Troika mirror on urbanoutfitters.com and in their storefronts," as they write. "The quality of Urban Outfitters' [knockoff] is an insult to our original Troika that we've been crafting and fine tuning since early 2013. We find it hard to believe that the design and dimensions (including the ledge for keepsakes) is a coincidence."
The pair are rightfully P.O.'d, and they've also taken the trouble to point out that design piracy affects a lot more than the designers. It's already got to be an awful feeling to see something you've worked on simply copied to profit others, but consider also the trickle-down effect this has on the other parties involved:
[The Troika is made from] sustainably harvested maple europly sourced from Anderson Plywood in Culver City, CA. Their staff is always very helpful and they carry a wide assortment of wood and finishes.
Our maple europly sheets are cut by Steve at Triumph Custom CNC and Laser Works, just down the street from our studio. Each piece is cut to size, the channel routed for the glass and then the edges are pre-sanded.
Our glass mirror is provided by a Armando's Glass in Hollywood, CA. This small, family owned shop has been in business for 40 years! Today, their son Luis now handles most of the heavy lifting, while his mom, Yolanda runs the shop.
When we first started producing Troikas, we were making our own boxes and foam corners for shipping. Eventually, we figured that our time was better spent making the Troika and not the packaging. We decided to invest in a large order of boxes and custom foam corners from Acorn Paper Products.
These are four local businesses that M.F.E.O patronizes. If the Van Hollands' sales are cannibalized by Urban Outfitters—whom they cannot hope to compete with in terms of reach and economies of scale—all five parties will suffer. And the Van Hollands are already feeling the effects, in a rather nasty way:
We recently put in the largest order from each of our local vendors because we were supposed to wholesale the maple europly Troika through another retailer. When we discovered the Urban Outfitters infringement, we notified our retailer in an effort to be forthright and transparent. They decided to postpone our contract and we're now sitting on 200+ Troikas waiting to be assembled and sold. If we can't continue to sell the Troika because of Urban Outfitters' knockoff, it not only impacts our business, but it affects each of our vendors as well.
Of all the things you'll do in the shop, sanding is often one of the least pleasant tasks. It's not the dust: It's the frustration of figuring out how to get sandpaper to follow the peculiar contours, crevices and cavities of your design. If you were sanding flat panels all day long, it'd be no problem; but the client isn't paying you to design flat panels.
Well, help is here, in a way that lets you see what several decades worth of shop time can yield. Master maker Jimmy Diresta runs through about two dozen brilliant sanding and scraping tips, using not just sandpaper but glass, rubber, Windex, metal weights, old utility knife blades, a pocket notebook and several other surprising items that will make your work go way quicker:
Rows of brightly colored PLA and rapid-prototyped pieces filled New York's Javits Center the other week for the annual 3D Print Design Show. The expo, which has been traveling internationally since 2012, invites manufacturers and makers alike to share their latest creations. It was there that the work of the Czech artist Helena Lukášová caught my eye. A blood-red, thorn-covered mask and a fur coat adorned with delicate gold arms and legs stood out in stark contrast to the LARPing helmets and novelty key-chains filling many of the booths.
Initially trained in fresco painting, mosaic making and woodworking techniques at the Academy of Fine Arts and Design in Bratislava, Slovakia, Lukášová became fascinated with digital additive and subtractive processes following a stint at the Johnson Atelier Technical Institute of Sculpture in New Jersey. Lukášová watched closely as sculptors at the facility used CNC-milling machines to produce work for clients. "It was just after the Velvet Revolution in our country—the society changed from the domination of communism to an open society," explains the Czech artist, who received her MFA in 1996. "The change in education I have experienced during my studies was also a revolution in a way. This experience keeps me aware of the fact that things can change and be totally different, be it in a conceptual meaning or in technology." The experience eventually inspired her to return to the Czech Republic and, in 2005, begin PhD studies with a focus on digital sculpture.
"I did very detailed research on that topic, which was not easy, as there was no representative publication about digital fabrication," the artist says. Lukášová's first printed piece was a tiny print of a female figure sitting on a pedestal overlooking a huge visualization of herself, called She About Herself in One Person. The artist continued to explore the medium, using a mix of photogrammetry, 3D scanning, 3DS Max and Mudbox to digitally build out her designs before sending them to be printed at Printed Nest, a prototyping community with workshops around the world, including in her city of Brno, Czech Republic. "Patience, patience, patience," Lukášová says, describing what it takes to build these pieces. "I learned it by doing embroidery. Modeling on the computer is time consuming and very meditative for me."
In her latest work, Lukášová tries to come up with concepts that require 3D printing for the final fabrication. At the 3D Print Design Show, Lukášová presented two projects created in collaboration with the fashion designer Denisa Nova. The aforementioned blood-red mask, called Cordyceps, was one of 15 in a series for the presentation of Nova's Spring/Ssummer 2014 collection; a series of 3D-printed clothing and heels, called You Are What You Wish For, was made for the designer's Autumn/Winter 2015/16 collection.
"We had great interdisciplinary experience working together," Lukášová says. "The human body has always been very interesting to me. I took molds of my own body, creating sort of human skins, then worked with the trajectories of the movement of the body in space using motion capture." For Cordyceps, which takes its name from the parasitic fungi, Lukášová built structures that represented different stages of growth, pulling inspiration from the growth of crystals, coral, coal and symbiotic colonies. (With real-life Cordyceps, spores attack living insects, then grow into beautiful, suffocating structures that eventually take the life of their host.)
The second series the duo presented, You Are What You Wish For, consisted of tiny gold body parts adorning various items of clothing. Lukášová used a 3D scanner and photogrammetry to scan and create digital files of the closest members of her family. "Digital tools let us work with 3D images that are charged with a lot of personal emotions and intimacy," she says. "These are just like photos of loved ones carried around in your purse." After printing out the scans, the artist applied gold leaf to the surface of the pieces, also treating the heels with a gold finish. "The 3D print loses its technical plastic look, and the gold makes the print lines more pronounced, thus creating an object which has a very antique feel without trying to mask its digital origin," Lukášová explains. The final golden limbs were then adhered to an old Persian coat Nova obtained in Belgium before painstakingly restoring it to its original state.
Lukášová sees the repurposed piece as extending the life of items that otherwise would be discarded. In the case of the Persian coat, the rare fur comes from baby Karakul lambs. "This is, of course, ethically not acceptable," she says. "To work with such a precious material, the remains of creatures once living their short lives, means to extend the existence of their physical presence." For Lukášová, the coat also brings to mind thoughts of Europe's troubled history in the 20th century, emphasized by hanging gilded arms and legs from the animal's hide.
As an artist using this medium, Lukášová often finds herself grappling with the conflict between creating unique works of art and the fact that these pieces can be endlessly duplicated. "Do I really want to print an infinite number of pieces?" she wonders. "Do I want to create limited editions? How do I protect my designs? Should I destroy my digital file at some point to ensure that more pieces cannot be recreated? The fine art [world] is more sensitive to the number of the copies of a piece, which compromises its uniqueness."
The artist balances those conflicts by introducing variations into her work, rendering each piece different from the last. By manipulating the file or pushing her digital models to the limit of what the printer is capable of, Lukášová is able to create imperfections that range from gaps and holes to jagged strings of plastic that cling to the final print. In many ways, the process can be likened to collaborating with the machine itself, as the internal robotics try to make sense of the 3D model, each time deviating from the file to find a new solution with uncontrolled results.
"I think we will see a lot of applications for parametric manipulation of the digital file for printing generative variations in the future," Lukášová says. "New and creative software are very important to develop this idea further." We'll stay tuned for next year's exhibition to see what the artist comes up with next.
Much of our electricity bills are spent countering nature: We turn on lights when it's dark, we make warm things cold, or cold things hot. If we could work with nature rather than against it, both our wallets and the environment would benefit in the long run.
Enter the Groundfridge. Designed by Floris Schoonderbeek for Dutch label Weltevree, whom we last caught at Dutch Design Week, this prefabricated root cellar keeps things at a constant 10 degrees Celsius. Not quite as chilly as the average refrigerator's 40 F (about 4.5 C), but the Groundfridge maintains its temperature using nothing more than the earth you bury it in.
Where it really shines is capacity. Made from polyester laminated around what looks to be a plywood core, the globular portion of the Groundfridge is 2.2 meters in diameter. This translates to a whopping 3,000-liter capacity; for scale, a huge American refrigerator with a 30-cubic-foot capacity translates to 850 liters. And again, the Groundfridge stays cool with no electricity (although it presumably uses some to power the included lights inside; the company doesn't mention how those are wired or what sort of lights they are).
There's no word on the price, but Weltevree expects to begin shipping them this summer.
Via Inhabitat
"Face hacking" might not have an artistic ring to it, but it looks stunning in execution. A collaboration between a multimedia artist, a makeup artist and a digital image engineer—Nobumichi Asai, Horoto Kuwahara and Paul Lacroix, respectively—has yielded Project Omote, which combines face-tracking technology with projection mapping to change people's faces in real-time. Here's the inaugural effort, developed last year and using model Yuka Sekimizu:
"Technically, it's very difficult to project with real-time tracking," writes Asai.
Nobody has done it before, so we had to start from scratch. The process was complicated, capturing with sensors, processing the data, creating CG renderings, and using projectors. Getting the timing right was also challenging, fixing delays and making sure the projection technology had the maximum precision to get the face and visuals matched.
…We used OptiTrack sensors for [their] speedy response, and developed original programs [in] C++. To [minimize] latency (delay), we devised ways to integrate the whole process into one program. This creates amazing effects.
This year the team pushed the effects further, using members of the J-pop band SMAP:
You can read more about the project here.
In just a few years, we've seen solar-powered cooking devices go from relatively cumbersome, outdoorsy objects to a refined product design that's ready for prime time.
The first commercially-successful solar oven we saw was the SolSource, developed in the Himalayas and successfully Kickstarted in 2013 by One Earth Designs. That same year, inventor Patrick Sherwin had his solar-powered, camping-sized GoSun Stove Kickstarted.
Like the Groundfridge, both of these devices work with nature to eliminate the need for electricity or fuel. Where they differ is in size: The SolSource has a large satellite-dish form factor whereas the camping-minded GoSun Stove is roughly the size of a rolled-up yoga mat.
Now Sherwin has split the difference, refining his initial design and scaling it up to create the GoSun Grill.
The design is fantastic: The food is cooked in a glass vacuum-walled cylinder which remains cool to the touch even as the sun roasts (or bakes, steams or boils) the food within. The reflectors cook the food from all sides, as if it had been roasted on a spit.
And Sherwin has added a crucial trick to this one: An on-board battery that can store two hours' worth of heat, meaning you can even cook at night.
We're pretty impressed at how quickly the solar-powered stove's design has progressed in just a couple of years. If the video's to be believed, this truly looks like it's ready for the mass-market in both developing and developed nations.
Backers agree. The GoSun Grill has already been successfully funded ($178,00 over $140,000) with 42 days remaining. And this despite the not-exactly-cheap price: The Early Bird buy-in without the battery is US $349 (expected to retail for $549); the with-battery units are going for $449 (MSRP a hefty $699). Sun-loving chefs are expected to have the first units by September of this year.
IDEO's known for forward thinking, and with their Automobility project, IDEO skipper Tim Brown shows what it really means to re-think something: Stepping back to reimagine not just transportation, but what we even use it for in the first place. The bulk of you travel to get to work; but what if you traveled inside of your workplace?
As confidence grows in autonomous ways of delivering goods and autonomous driving becomes more mainstream, a third stage of automobility will come into existence. It will involve inverse commutes, where working spaces come closer to where people live instead of commuters heading to pre-determined workplaces.
The WOW concept is at least as fascinating as it is far-out. A Columbia University Earth Institute study cited in IDEO's research reveals that U.S. cities have some 600 million parking spaces taking up 10% of the available land. The proposal calls for turning these spaces into "Automobility work nexuses," where WOW vehicles could dock. Alternatively, the vehicles could travel to different locations depending on the work:
As more work moves to the digital realm, boardrooms and other traditional office infrastructure will be less necessary. For those times when face-to-face interaction is important, a WOW pod can provide a flexible space for workers to gather. WOW pods might occupy a location between two offices, splitting travel times for both teams, or could be parked by a site-specific project, like a building under construction or a gallery where an exhibition is being installed.
Read the entirety of the fascinating proposal here.
Name:Tad Toulis
Occupation: Designer, and I'm the vice president of design at Sonos
Location: Santa Barbara, California
Current projects: You know I can't give you an answer to this question. [Laughs] The projects I'm working on are all various aspects of how we try to extend the mission of Sonos, which is to deliver the ultimate home-music experience. So we're working on ways of reinventing and keeping fresh that mission in a marketplace where streaming is becoming more and more relevant.
Mission: Sonos has this wonderful statement, which is that we deeply believe that music makes a house a home. So the way I think of design at Sonos is to get people to experience joy, and the interesting challenge is to create that experience through our hardware and software.
When did you decide that you wanted to be a designer? I grew up in New York City, and my father and mother taught at Pratt Institute. And when I was young, I used to go with my dad to work a fair amount. His department, which was print-making, was in the same building as the industrial design department. When I would get bored, I would wander around, and I would walk into these design studios where I would see objects that I knew from real life, but that looked more interesting than the ones I knew in real life. And I think that got me very curious about why people do that.
So I got exposed to it very young, and I had this deep interest that waxed and waned over the years. When I got done with my undergraduate degree, which was from Wesleyan University, I was fortunate enough to graduate into a really crappy economy, and I started auditing classes at Pratt. That's when I started falling back into a path that led me to becoming an industrial designer.
Education: At Wesleyan I was a fine arts and English lit major, and then at Pratt I eventually got a master's in industrial design.
First design job: My first real professional gig was just after Wesleyan; I somehow landed an internship at Milton Glaser Associates in New York. That was for graphic design. And then my first job after graduating from Pratt was at a medical manufacturer based in New Jersey.
Who is your design hero? I was dreading that question. There are a lot of designers whose work I really like, but my heroes actually tend to be in related industries. I get really jazzed about artists like Donald Judd or James Turrell, for instance. Any visual or artistic endeavor where you're re-filtering the culture around you through a creative lens—that really gets me going.
But I will also say that I'm very fond of Scandinavian design—and since I've been at Sonos, that has actually been one of the more resonant things to think about, because I think the Scandinavian designers do a great job of having a more poetic observation of the rational. Whereas German design is crazy rational—and everybody loves it for that—Scandinavian design has a bit more of a poetic mindset. It's still very clean and rational, but it has more humanity and subjectivity in it, if that makes sense.
Describe your workspace: We're in Santa Barbara, which is pretty amazing. I'm a big believer that environment impacts your work—years ago, I read an article about the Eameses, and it said that when they were leaving Cranbrook and deciding where to work, they went through the list of choices, and they didn't want to go to New York because they thought they would be too occupied by the social calendar; they didn't want to go to Chicago for the same reasons, and they felt like in Los Angeles they could get down to some really good work. And I feel like Santa Barbara is an awesome place to get down to some really good work. It's a little quiet at times, but LA's not that far away.
The Sonos facility is this classic Spanish Colonial–style building. So it's really charming—wooden floors, probably 1940s construction, light and airy and just a homey place to do design, which feels like a good place to be tackling the types of problems we're tackling.
Other than the computer, what is your most important tool? My curiosity. I think the best design tool I have is a deep curiosity that allows me to kind of naively go into problem spaces that maybe I don't know that much about, but also know how to navigate being naive and how to harness being naive.
I'm not particularly in love with technology—I think technology is an amazing tool that can do amazing things—but being a bit naive about how it all works actually helps me to keep more of an expectation of the end user. It kind of ties in to how Picasso said, "I've lived my whole life to learn how to draw like a child." There's a lot of truth to being super-experienced but still being able to tap into an almost naive perspective.
I'm not particularly in love with technology—I think technology is an amazing tool that can do amazing things—but being a bit naive about how it all works actually helps me to keep more of an expectation of the end user.
What is the best part of your job? Doing something every day that I'm really passionate about. More tactically, it's about working with people who are talented and helping to move groups of people through relatively ambiguous problems toward concrete results. The dynamic in design teams and creative teams—whether they're in the kitchen or in the theatre or in industrial design or product development—is there's so much interplay of personality and aspiration, that I think the best part of the job is just getting to spend lots of time with people who are great "pessimistic optimists." They can envision things that don't exist, and they can also do the hard work required to make those things happen. It took me a long time to realize that you have a big impact on culture when you do those things.
What is the worst part of your job? It's actually not that different from the best part. I think the worst part of the job is realizing how hard it is, and how exceptional it is, to communicate effectively across wide groups of people, in a way that supports the type of work we're trying to do. I think about this a lot. Like, someone can give a really good speech and resonate with people emotionally. And that certainly comes in handy when you're working with a big cross-section of people. But when you're trying to get those people tactically to achieve certain ends, it's not just about appealing to their hearts. And one of the things that never ceases to fascinate me is how much words have such different meaning to different people. Some people like to be very specific with their words, and that can be great, but it can also create huge disconnects.
So the thing that takes up the most time—and I wouldn't say I like it the least, but it's probably one of the greatest challenges—is figuring out how to be really effective in communication across technical teams, emotional teams, strategic teams. Because while they'll all get on board for a good story, the hard work happens a couple layers below that, and that's where stuff can either get pear-shaped or turn out really elegant.
What time do you get up and go to bed? I get up around 6:30 a.m., and I usually go to bed around 11:00 or 11:30 p.m. I try to squeeze in eight hours, because once I'm up, I just go; I'm all in until I go to bed again. And that takes a lot of energy and stamina. So I try to make sure that I capture as much of an eight-hour night as I can; otherwise, you're working from a deficit.
How do you procrastinate? Read e-mail. [Laughs] Or go to a meeting. That sounds a little unfair, but it's probably true. Because the ways that I used to procrastinate are now my pleasures—like, reading or surfing the web. And I feel like the real procrastination tools now are, like, "Well, I'll check some e-mail before I get going."
What is your favorite productivity tip or trick? I grew up in New York City, and I've lived now more than half my life on the West Coast. And the thing that used to surprise me here was that I would be having a bad day at the office, and then I would walk outside—and in Southern California, nine times out of ten it's gorgeous out—and that would give me a totally different orientation to the problem. That still works pretty well, and I've got to say that Santa Barbara is kind of ridiculous on that front. So my best trick is just walking outdoors and coming back inside.
What is the most important quality in a designer? Stamina and thick skin. Design is an activity where you're daring to think of something that doesn't exist. And that takes a certain amount of hubris. And you hear no so much, and you're told why things won't work so often, that at some point it really does engender people who don't seem to listen to that. And that's a strange trait; I think it happens because you just get immune to it. But I do think perseverance and stamina are tremendously important traits in being a designer.
What is the most widespread misunderstanding about design or designers? I think that one of the worst ones is something that some designers actually encourage, which is that somehow designers are these special entities endowed with a magical power. There is some nominal truth to the idea that we see things in a different way and we think differently than other parts of the culture. But there is logic inside of design—it's just not all logic. And so I think the myth is that somehow designers are, like, super-sentient beings on this unique wavelength, and they have to be handled in a certain way, and what they do is just intuitive.
What is your most prized design possession? It's hard for me to identify one thing. As I've gotten older, I don't really buy a lot of stuff. Increasingly, my most prized possessions are heirlooms or other things that have deep personal memory and associations for me. Like a sugar dispenser that my grandmother had in Cuba that my mother has used every day of my entire existence, and that every time I see it I think about it.
What is exciting you in design right now? There is an interesting thing happening where lots of parts of design are finally meeting. What's fascinating for me, and what I feel really blessed by, is to be in a problem space where I'm sitting across from the hardware/software part of that problem in a way that lets me see how these two camps of design—physical and digital—are actually in a place where they can meet relatively well. The nature of the problem right now for a lot of companies is we're trying to gin up experiences. And that is the sum of those parts; it's not one or the other.
If you could redesign anything, what would you choose? I don't really like to think that way. There are some things I've encountered that I think could be done better, but I feel like I'm always looking to "What's the next problem to be working on?" And I find it odd that we still train students to think that they're just going to make things, versus that they might make a few things, but maybe a lot of their career is going to be arguing why something shouldn't be made but still get paid for.
What do you hope to be doing in ten years? Pretty much the same thing. I really love this work; it's a deep passion and philosophy for me. It's about really remaining curious, remaining pessimistically optimistic, trying to figure out where things are going, trying to do them in a way that is meaningful to people—and also at some level, protecting people from technology a little bit.
Lastly, who's more fun to have a drink with: architects, industrial designers or graphic designers? Hands down, industrial designers. They're just an interesting group of people who have the same scar tissue. They tend to somehow bounce back regardless of what's happening. So they're a fun crowd to be with. But I'd be happy to have a beer with pretty much anyone, if they're paying for it.
Brittany Wright photographs everything from products and spaces to weddings and portraits. But our favorite part of the Seattle-based shooter's book is her series on food. "I'm working on my life goal of teaching myself how to cook everything and anything," Wright writes. "I enjoy the science behind cooking and experimenting with flavors. I see food as an art, and an opportunity to do something creative."
Thus Wright, who with her photographer's eye could not help but notice the different color gradations of food, began arranging and shooting them in ways that highlight this:
Food and color lovers can dive into her Instagram here.
Via Foodiggity
Like you, I figured this had to be a gag. But apparently the Golfboard is a legitimate golf-course-traversing vehicle, one that is "undeniably the most exciting and enjoyable way to experience any course." (I'd think a turf-destroying ATV might have it trumped, but then I'm not a golfer.)
Riders step onto the four-wheel-drive contraption and work the throttle via either a wireless remote or a button on the handle. The concave riding platform, which is actually modeled after a skateboard deck, handles the steering via the rider's leaning. The deck itself is mounted on two shock-absorbing springs, protecting the rider from the harsh jostling that comes from riding over painstakingly manicured grass. It tops out at a blistering 10 miles per hour.
As frivolous as it may seem, the company is hoping that their vehicle will actually reinvigorate interest in the very sport that the folks in the video are all saying takes too long to play.
Capitalizing on the current rapid growth in the popularity of board sports, the GolfBoard is perfectly positioned to have a revolutionary impact on golf by attracting a much-needed influx of the younger demographic, which will be so vital to the growth of the game. For this generation who has grown up with board sports of all kinds, GolfBoard will be the natural and preferred way to play golf.
I'm not sold, as it still presupposes an interest in golf in the first place. Golfers in the readership, what say you?
The Westminster Arcade in Providence is America's oldest existing shopping mall, with a structure dating back to 1828. As its fortunes began to wane in the late 1900s, the building was shuttered several times. But in 2008 a massive five-year renovation took place, and real estate developer Evan Granoff had a novel idea: Why not convert the upper floors into microapartments?
By 2013 the Arcade Providence Microlofts were on the market—with a waiting list. (To date, even the model unit has been rented.) The immensely popular microapartments, most of them just 225 square feet, line the second and third floors of the mall's gallery, exposed to the massive atrium's skylights. Independent designer fashion brands (no major labels allowed) fill out the ground-floor retail spaces, creating a unique vibe.
So what do the spaces actually look like inside, and what types of people live there? Have a look:
Casino carpeting is pretty ugly, but the hideous floor covering at Portland International Airport gives it a run for its money. So lovably awful is PDX's carpet that it's spawned an Instagram account with nearly 20,000 followers re-gramming the "outdated, unfashionable, and absolutely charming" surface; it has its own Facebook page; it has its own Wikipedia entry.
And it's spawned a cottage industry. Website PDX Carpet sells T-shirts, pillows, posters and tote bags emblazoned with a facsimile of the pattern. Made in Oregon sells PDX-carpet-looking socks, keychains, hats, mugs and even infant onesies. Outdoor gear manufacturer Keen sells their Yogui slip-on footware in just one color—"PDX Carpet." Belle Helmets lets you protect your noggin, and Namu Designs lets you protect your phone, with PDX carpet style.
Not to mention you can buy pieces of the actual carpet itself.
That's because it dates back to 1987, and it's now in the process of being replaced. (The changeover should be complete by Thanksgiving of this year.) "We understand," Port of Portland spokeswoman Annie Linstrom told Portland Monthly, "that people have an emotional connection to the carpet." And while the new pattern looks similar (see below) to the old, it isn't quite the same.
As for the design of the original carpet itself,
Designed by SRG Architects in 1987, the iconic carpet was a big change for the Port of Portland.
…SRG principal John Schleuning (who helped design the carpet) recalls visiting at least five different airports before buckling down to design the PDX carpet.
…Earth tones (think beige and oatmeal) were standard for airport carpets in the 80s, Schleuning says. Indeed, he says one airport chose its dull carpet color to blend in with fallen cigarette butts.
The SRG team wanted the carpet to be northwest to the core, so they settled on blues and greens early on in the design phase. The final pattern corresponded to Portland's intersecting North-South runways, as seen from the control tower.
And here's the incoming stuff:
The new design is based on organic and man-made shapes found around the airport, referencing flight, nature and structures at PDX.
"The Port hopes that travelers will grow to appreciate elements of the new carpet design over time, just as much as the old," says Linstrom.
We're not sure that's gonna happen.
To demystify the process of working with a CNC mill, here we'll show you what you need to learn to cut a basic part out. In broad strokes, there are four steps:
1. Setting up the drawing file
2. Converting your drawing into toolpaths
3. Mounting the bit & workpiece
4. Cutting the part
A CNC mill offers you an amazing amount of options within those four steps, and in future episodes we can drill down into them further; but for now we wanted to ease you into it, so think of this as more of an overview.
We're making appleboxes for our first project, starting with the top and bottom pieces, which require both straight profile cuts and rounded edges. Here we go:
Admittedly, flipping a store sign from "Open" to "Closed" isn't a huge difficulty. But it still tickles us that this man came up with a more kinetically interesting way to change one to the other:
Fine, so he left the "D" out and the "N" is backwards. The meaning is still clear.
The strange thing is that the inventor, Ikeda Yosuke , isn't a designer at all—but a mime. No white makeup and striped shirt, but a professional mime nonetheless. And interestingly enough, he incorporates graphic design and typography into his performances:
We know pantomime isn't everyone's cup of tea, but if you enjoyed either of the videos above, you'll want to take a look at some of Ikeda's pieces.
Industrial designer Jessica Chan was working on a sustainable printer concept when she made an interesting discovery: "I learned that inks—even those made with vegetable and soy—used in traditional printers are not 100% biodegradable," writes Portland-based Chan. "I [subsequently] re-evaluated my approach toward product design as a whole and began taking into consideration the full cycle of products; everything from how materials are first sourced to the manufacturing processes, as well as environmental footprints pre- and post-consumer use."
This led her down the path of using ink alternatives, and designing a vessel to deliver them: The WINKpen.
By designing a glass nib, Chan created a pen can dispense unlikely "inks" like wine (hence the name, from "wine as ink"), beer, tea, and even liquid condiments. She also designed the pen to be easy to clean and reload:
Having sunk some $13,000 of her own money into the project, Chan is now seeking to crowdsource production:
At press time the Kickstarter campaign was at $7,404 of a $47,000 goal, but there was still more than a month left. To get it over the hump, perhaps a more specific range of folk need to be targeted, like:
- Banks. Previously it was inconvenient to have borrowers sign their mortgages in blood, but this removes that barrier.
- Hip Hop Moguls. Because how pimp would it be to sign million-dollar checks with an ultraexpensive Burgundy?
- Frequent Fliers. Your plane is seventh in the queue to take off, and the snippy flight attendant isn't willing to break protocol and break out the drinks cart until you're at cruising altitude. Sure would be nice to reach into your pocket for a little backup hooch….